Your Ultimate Guide to Sourcing Heavy Duty Industrial Air
Introduction: Navigating the Global Market for heavy duty industrial air compressor
In today’s competitive industrial landscape, heavy-duty industrial air compressors are indispensable assets for businesses aiming to enhance productivity and efficiency. These robust machines are designed to deliver powerful, reliable compressed air for a wide range of applications, from manufacturing and construction to automotive and energy sectors. As global industries evolve, the demand for advanced air compressor solutions continues to rise, making it critical for B2B buyers to understand their options thoroughly.
This comprehensive guide is tailored for international B2B buyers, especially from Africa, South America, the Middle East, and Europe, including regions like South Africa and Indonesia. It explores various types of heavy-duty industrial air compressors, such as rotary screw, reciprocating, and oil-free models, alongside the materials and manufacturing quality standards that impact performance and longevity.
Buyers will find detailed insights on sourcing from reputable suppliers, evaluating cost factors, and understanding market trends. The guide also addresses common FAQs, empowering decision-makers to make informed choices that align with their operational needs and budget constraints.
By leveraging the knowledge presented here, businesses can confidently navigate the global market for heavy-duty industrial air compressors, ensuring they select the right equipment that maximizes efficiency and drives long-term success.
Understanding heavy duty industrial air compressor Types and Variations
Type Name | Key Distinguishing Features | Primary B2B Applications | Brief Pros & Cons for Buyers |
---|---|---|---|
Reciprocating Compressors | Piston-driven, typically louder, available in single or two-stage models | Small to medium-sized businesses, automotive shops | Pros: Cost-effective, simple maintenance. Cons: Noisy, less efficient for continuous operation. |
Rotary Screw Compressors | Continuous operation, quieter, energy-efficient, often equipped with variable-speed drives | Manufacturing, construction, heavy-duty applications | Pros: High efficiency, low maintenance. Cons: Higher initial cost, requires more space. |
Oil-Free Scroll Compressors | Oilless design, quiet operation, low maintenance needs | Pharmaceutical, food processing, electronics | Pros: Clean air supply, energy-efficient. Cons: Limited pressure range, potentially higher upfront costs. |
Centrifugal Compressors | Uses centrifugal force, suitable for high volume and pressure | Large industrial plants, power generation | Pros: High efficiency for large volumes, minimal maintenance. Cons: High initial investment, complex installation. |
Portable Compressors | Compact, mobile, often diesel-powered for outdoor use | Construction sites, remote applications | Pros: Versatile, easy transport. Cons: Limited power output, may require fuel management. |
Reciprocating Compressors
Reciprocating compressors operate using pistons and are commonly found in small to medium-sized businesses. These compressors can be single-stage or two-stage, with the latter providing better efficiency and pressure capabilities. Buyers should consider the noise level, as these units tend to be louder than others. They are cost-effective and easy to maintain, making them suitable for businesses with moderate air demands.
Rotary Screw Compressors
Rotary screw compressors are designed for continuous operation, making them ideal for industries with high air demand. They feature a quieter operation and often come equipped with variable-speed drives to optimize energy consumption. While they may require a higher initial investment, their efficiency and low maintenance needs can lead to significant long-term savings. Buyers should assess their space requirements and ensure they have the necessary infrastructure for installation.
Oil-Free Scroll Compressors
These compressors are designed for applications requiring clean, oil-free air, making them suitable for industries like pharmaceuticals and food processing. Their oilless design results in quieter operation and minimal maintenance needs. While they can be more expensive initially, the benefits of energy efficiency and reduced contamination risk make them a valuable investment. Buyers should evaluate their specific air quality requirements and potential long-term savings.
Centrifugal Compressors
Centrifugal compressors utilize centrifugal force to compress air, making them suitable for high-volume and high-pressure applications. They are commonly used in large industrial plants and power generation. Their efficiency and low maintenance requirements are significant advantages. However, buyers must be prepared for a higher initial investment and a more complex installation process. Understanding the specific air demand and operational needs is crucial before purchasing.
Portable Compressors
Portable compressors are compact and designed for mobility, often powered by diesel engines for use in outdoor environments. They are commonly employed in construction sites and remote applications where a stationary compressor is impractical. While they offer versatility and ease of transport, their power output may be limited compared to stationary models. Buyers should consider their specific application needs and fuel management capabilities when selecting a portable compressor.
Related Video: How does an Air Compressor work? (Compressor Types) – Tutorial Pneumatics
Key Industrial Applications of heavy duty industrial air compressor
Industry/Sector | Specific Application of heavy duty industrial air compressor | Value/Benefit for the Business | Key Sourcing Considerations for this Application |
---|---|---|---|
Manufacturing | Powering pneumatic tools and machinery | Increases productivity and efficiency in production lines | Reliability, maintenance support, and energy efficiency ratings |
Automotive | Spray painting and surface preparation | Ensures high-quality finishes and reduces rework costs | Compatibility with existing systems and noise levels |
Construction | Concrete mixing and pneumatic conveying | Enhances workflow and reduces labor costs | Portability, durability, and pressure capabilities |
Oil & Gas | Drilling and extraction processes | Maximizes operational uptime and safety | Compliance with industry standards and energy consumption |
Food & Beverage | Packaging and processing applications | Maintains product quality and safety standards | Hygiene compliance, oil-free operation, and energy efficiency |
Manufacturing
In the manufacturing sector, heavy duty industrial air compressors are essential for powering pneumatic tools and machinery, such as drills, lathes, and conveyor systems. These compressors provide the necessary air pressure to operate tools efficiently, which enhances productivity on the production line. International buyers should consider the reliability and maintenance support of the compressor, as well as its energy efficiency ratings, to ensure long-term operational effectiveness and reduced energy costs.
Automotive
Within the automotive industry, heavy duty air compressors are widely used for spray painting and surface preparation. The ability to deliver consistent air pressure allows for high-quality finishes and minimizes the risk of imperfections that could lead to costly rework. B2B buyers should evaluate the compatibility of the compressor with existing systems and consider noise levels, as quieter operations can improve the working environment in autobody shops.
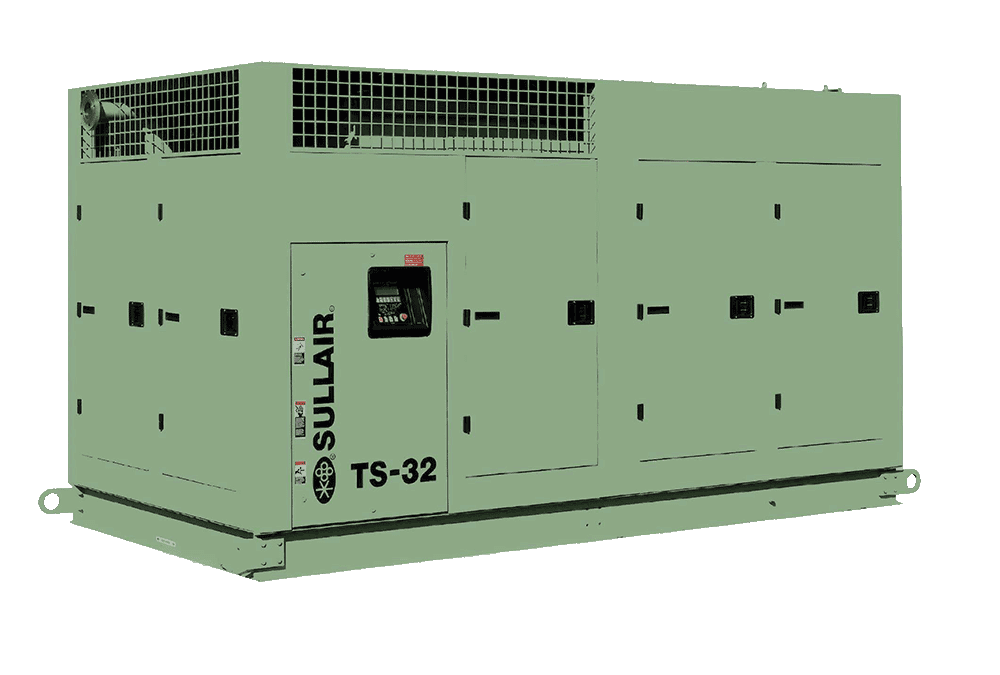
Illustrative Image (Source: Google Search)
Construction
In construction, heavy duty air compressors are utilized for concrete mixing and pneumatic conveying, which streamlines workflows and reduces labor costs. These compressors facilitate the efficient movement of materials and tools on-site, ensuring projects remain on schedule. When sourcing compressors for construction, buyers should prioritize portability, durability, and pressure capabilities to withstand the rigors of demanding job sites.
Oil & Gas
The oil and gas sector relies on heavy duty industrial air compressors for drilling and extraction processes. These compressors maximize operational uptime and enhance safety by ensuring reliable air supply for various tools and equipment. Buyers in this industry must consider compliance with industry standards and energy consumption rates, as these factors can significantly impact operational costs and regulatory adherence.
Food & Beverage
In the food and beverage industry, heavy duty air compressors play a vital role in packaging and processing applications. They help maintain product quality and adhere to safety standards by providing clean, oil-free air for processes such as bottling and canning. Buyers should focus on hygiene compliance, ensuring that the compressors are designed for oil-free operation, and evaluate energy efficiency to reduce operational costs in this highly regulated sector.
Related Video: Project ‘Poo Zoo’ uses animal dung to save at-risk species | REUTERS
Strategic Material Selection Guide for heavy duty industrial air compressor
When selecting materials for heavy-duty industrial air compressors, it is crucial to consider the properties and performance characteristics that directly impact efficiency, durability, and overall application suitability. Below is an analysis of four common materials used in the construction of these compressors, focusing on their key properties, advantages, disadvantages, and specific considerations for international B2B buyers.
1. Cast Iron
Key Properties:
Cast iron is known for its excellent compressive strength and ability to withstand high temperatures and pressures. It typically has a temperature rating up to 400°F (204°C) and can handle pressures exceeding 150 psi.
Pros & Cons:
– Pros: Highly durable and resistant to wear, making it suitable for long-term use in demanding environments. It also has good vibration dampening properties.
– Cons: Heavier than other materials, which can complicate transportation and installation. It may also be more susceptible to corrosion if not properly maintained.
Impact on Application:
Cast iron is ideal for applications requiring high durability and resistance to mechanical stress, such as in manufacturing and heavy machinery.
Considerations for International Buyers:
Buyers should ensure compliance with local standards such as ASTM or DIN for material specifications. In regions with high humidity, additional corrosion protection may be necessary.
2. Aluminum
Key Properties:
Aluminum is lightweight and possesses good thermal and electrical conductivity. It can operate effectively at temperatures up to 350°F (177°C) and pressures around 100 psi.
Pros & Cons:
– Pros: Its lightweight nature facilitates easier installation and transport. Aluminum also offers excellent corrosion resistance, making it suitable for various environments.
– Cons: Generally less durable than cast iron, particularly under high-stress conditions. It may also be more expensive due to processing costs.
Impact on Application:
Aluminum is particularly advantageous in applications where weight savings are critical, such as portable compressors or in industries like automotive and aerospace.
Considerations for International Buyers:
Buyers should verify that aluminum components meet relevant quality standards and consider the impact of local environmental conditions on material performance.
3. Stainless Steel
Key Properties:
Stainless steel is renowned for its corrosion resistance and ability to withstand high temperatures (up to 1500°F or 815°C) and pressures (up to 300 psi).
Pros & Cons:
– Pros: Exceptional durability and resistance to corrosion make it ideal for harsh environments, including those with exposure to chemicals.
– Cons: Higher cost compared to other materials and can be more challenging to machine, leading to increased manufacturing complexity.
Impact on Application:
Stainless steel is suitable for applications that require clean air, such as food processing and pharmaceuticals, where contamination is a concern.
Considerations for International Buyers:
Compliance with international standards for food-grade materials is essential. Buyers should also assess local availability and costs associated with stainless steel components.
4. Composite Materials
Key Properties:
Composite materials often combine fibers and resins to create lightweight, strong components with good thermal stability. They can operate effectively at temperatures up to 300°F (149°C) and pressures around 150 psi.
Pros & Cons:
– Pros: Lightweight and resistant to corrosion, composites can be tailored for specific applications, enhancing performance.
– Cons: They may have lower strength compared to metals and can be more expensive due to advanced manufacturing processes.
Impact on Application:
Composites are increasingly used in specialized applications such as aerospace and automotive, where weight reduction is critical.
Considerations for International Buyers:
Buyers should ensure that composite materials meet relevant international standards and consider the implications of local manufacturing capabilities.
Summary Table
Material | Typical Use Case for heavy duty industrial air compressor | Key Advantage | Key Disadvantage/Limitation | Relative Cost (Low/Med/High) |
---|---|---|---|---|
Cast Iron | Heavy machinery and manufacturing applications | Highly durable and wear-resistant | Heavier, potential corrosion risk | Medium |
Aluminum | Portable compressors in automotive/aerospace industries | Lightweight and corrosion-resistant | Less durable under high stress | Medium to High |
Stainless Steel | Food processing and pharmaceuticals | Exceptional corrosion resistance | Higher cost and machining complexity | High |
Composite Materials | Aerospace and specialized automotive applications | Lightweight and customizable | Lower strength compared to metals | Medium to High |
By understanding the properties and implications of these materials, international B2B buyers can make informed decisions that align with their operational needs and regional standards.
In-depth Look: Manufacturing Processes and Quality Assurance for heavy duty industrial air compressor
When considering the purchase of heavy-duty industrial air compressors, international B2B buyers must gain a comprehensive understanding of the manufacturing processes and quality assurance practices that underpin these critical machines. This knowledge not only aids in evaluating suppliers but also ensures that the compressors meet operational needs and compliance standards.
Manufacturing Processes for Heavy-Duty Industrial Air Compressors
The manufacturing process of heavy-duty industrial air compressors typically consists of four main stages: material preparation, forming, assembly, and finishing. Each stage plays a crucial role in determining the performance, durability, and efficiency of the final product.
1. Material Preparation
The first stage involves selecting high-quality raw materials, such as cast iron, aluminum, and various alloys, which are essential for the durability and performance of air compressors. The materials are rigorously inspected and tested to ensure they meet specific industry standards.
- Key Techniques:
- Material Testing: Conducting tensile, hardness, and impact tests to verify the material’s properties.
- Supplier Certification: Ensuring that materials are sourced from certified suppliers who comply with international standards.
2. Forming
In the forming stage, raw materials are transformed into compressor components using various techniques, including casting, machining, and forging.
- Key Techniques:
- Casting: Components such as compressor housings are often produced via sand or investment casting to achieve complex shapes.
- Machining: Precision machining processes, such as CNC milling and turning, are employed to achieve tight tolerances for moving parts.
- Forging: Critical components like crankshafts may be forged for enhanced strength and fatigue resistance.
3. Assembly
The assembly stage involves integrating all components into a cohesive unit. This process requires precision and expertise to ensure that each part functions harmoniously.
- Key Techniques:
- Automated Assembly: Utilizing robotic systems for consistent and accurate assembly of components.
- Manual Assembly: Skilled technicians perform final adjustments and inspections to ensure quality and performance.
4. Finishing
The finishing stage involves surface treatments and coatings to enhance the compressor’s durability and resistance to wear and corrosion.
- Key Techniques:
- Painting and Coating: Application of protective coatings to prevent rust and corrosion.
- Polishing: Surface polishing for aesthetic appeal and to minimize friction in moving parts.
Quality Assurance Practices
Quality assurance (QA) is integral to the manufacturing of heavy-duty industrial air compressors. It ensures that products meet stringent performance standards and compliance with international regulations.
International Standards
Many manufacturers adhere to international quality standards such as ISO 9001, which provides a framework for consistent quality management practices. In addition, industry-specific certifications may include:
- CE Marking: Indicates compliance with EU safety, health, and environmental protection standards.
- API Standards: Relevant for compressors used in oil and gas applications, ensuring adherence to specific performance and safety criteria.
Quality Control Checkpoints
Quality control (QC) checkpoints are established throughout the manufacturing process to monitor and verify quality at various stages:
- Incoming Quality Control (IQC): Inspecting raw materials upon arrival to ensure compliance with specifications.
- In-Process Quality Control (IPQC): Continuous monitoring during the manufacturing process to identify and rectify issues early.
- Final Quality Control (FQC): Comprehensive testing of the finished product to confirm that it meets performance and safety standards.
Common Testing Methods
Manufacturers employ several testing methods to validate the performance and reliability of heavy-duty industrial air compressors:
- Performance Testing: Evaluating airflow, pressure, and power consumption under various operating conditions.
- Durability Testing: Subjecting compressors to stress tests to simulate real-world conditions and assess longevity.
- Noise Level Testing: Measuring noise emissions to ensure compliance with environmental regulations.
Verifying Supplier Quality Control
International B2B buyers, especially those from Africa, South America, the Middle East, and Europe, should take proactive steps to verify the quality assurance practices of potential suppliers.
- Supplier Audits: Conducting on-site audits to assess manufacturing capabilities, quality control processes, and compliance with international standards.
- Quality Reports: Requesting detailed quality reports that outline testing results, certifications, and compliance with relevant standards.
- Third-Party Inspections: Engaging independent inspection agencies to evaluate the manufacturing process and product quality before shipment.
Quality Control and Certification Nuances for International Buyers
When purchasing heavy-duty industrial air compressors, buyers must be aware of the following nuances:
- Local Regulations: Understanding the specific regulations and standards applicable in their country can affect the choice of supplier and product.
- Documentation: Ensuring that all necessary documentation, including compliance certificates and quality reports, is available and valid.
- Supplier Relationships: Building strong relationships with suppliers can facilitate better communication regarding quality expectations and compliance issues.
Conclusion
Understanding the manufacturing processes and quality assurance practices for heavy-duty industrial air compressors is crucial for international B2B buyers. By focusing on material quality, manufacturing techniques, and robust quality control measures, buyers can make informed decisions that align with their operational needs and ensure compliance with international standards. Investing time in supplier verification not only mitigates risks but also fosters long-term partnerships that can enhance operational efficiency and profitability.
Related Video: Amazing Process of Making Tea Kettle from Recycled Aluminium Rusted Scrap | Mass Production
Comprehensive Cost and Pricing Analysis for heavy duty industrial air compressor Sourcing
When sourcing heavy-duty industrial air compressors, understanding the comprehensive cost structure and pricing factors is crucial for international B2B buyers. This analysis will enable buyers from regions such as Africa, South America, the Middle East, and Europe to make informed purchasing decisions.
Cost Components
-
Materials: The cost of raw materials is a significant portion of the overall expense. Components such as aluminum, steel, and specialized alloys used in the manufacture of air compressors can fluctuate in price based on global market conditions. For buyers, it’s vital to assess the material quality and its impact on performance and longevity.
-
Labor: Labor costs vary widely depending on the manufacturing location. Regions with lower labor costs can offer more competitive pricing. However, it’s essential to balance this with the skill level of the workforce, as higher quality craftsmanship can lead to reduced maintenance costs in the long run.
-
Manufacturing Overhead: This includes utilities, rent, and equipment depreciation. Efficient manufacturing processes can mitigate these costs, ultimately affecting the price of the finished product. Buyers should inquire about a supplier’s operational efficiency as it can influence the pricing structure.
-
Tooling: Custom tooling for specific compressor designs can add to the initial costs. However, investing in proper tooling can lead to better precision and lower defect rates, which is a crucial consideration for long-term reliability.
-
Quality Control (QC): Rigorous QC processes ensure the compressors meet industry standards and specifications. While this may increase upfront costs, it can significantly reduce the risk of failure and warranty claims, translating to lower Total Cost of Ownership (TCO) for the buyer.
-
Logistics: Shipping costs, including freight and insurance, must be factored into the total price. International buyers should consider the distance from the supplier, transportation methods, and any tariffs or customs duties that may apply.
-
Margin: Suppliers will typically include a profit margin in their pricing. Understanding the typical margins in the industry can provide leverage during negotiations.
Price Influencers
-
Volume/MOQ (Minimum Order Quantity): Larger orders often lead to better pricing. Buyers should consider their operational needs and future growth to negotiate favorable terms.
-
Specifications/Customization: Custom features or specifications can increase costs. Buyers should clearly define their requirements to avoid unnecessary expenses.
-
Materials and Quality Certifications: High-quality materials and certifications (e.g., ISO, CE) can justify higher prices. Buyers should assess whether these certifications align with their operational needs.
-
Supplier Factors: Reputation, reliability, and experience of the supplier can significantly impact pricing. Established suppliers may charge a premium but often provide greater assurance of product quality and support.
-
Incoterms: Understanding Incoterms (International Commercial Terms) is essential for international buyers. These terms define responsibilities regarding shipping, insurance, and tariffs, impacting the total cost.
Buyer Tips
-
Negotiation: Engage suppliers in discussions about pricing and terms. Leverage multiple quotes to foster competition and potentially lower prices.
-
Cost-Efficiency: Analyze the TCO, which includes purchase price, maintenance, energy consumption, and potential downtime. A lower upfront cost may lead to higher long-term expenses.
-
Pricing Nuances: Be aware that prices may vary significantly based on regional factors. For instance, currency fluctuations, import tariffs, and local market demand can all influence costs in Africa, South America, the Middle East, and Europe.
-
Disclaimer for Indicative Prices: Prices for heavy-duty industrial air compressors can vary widely based on the factors mentioned above. Always seek detailed quotes tailored to your specific needs and circumstances.
By carefully analyzing these cost components and pricing influencers, B2B buyers can make strategic purchasing decisions that align with their operational requirements and budget constraints, ensuring the best value from their investment in industrial air compressors.
Essential Technical Properties and Trade Terminology for heavy duty industrial air compressor
Understanding the technical specifications and trade terminology related to heavy-duty industrial air compressors is crucial for B2B buyers to make informed purchasing decisions. This section outlines essential properties and jargon that can significantly impact your acquisition strategy.
Key Technical Properties
-
Cubic Feet per Minute (CFM)
– Definition: CFM measures the volume of air the compressor can deliver in one minute.
– Importance: Understanding CFM is vital to ensure the compressor meets the air demands of your operations. Insufficient CFM can lead to inefficiencies and operational delays. -
Horsepower (HP)
– Definition: HP indicates the power output of the compressor’s motor.
– Importance: Higher HP ratings generally correlate with increased CFM. For heavy-duty applications, selecting the right HP ensures that the compressor can handle the workload without overheating or failing. -
Pressure Rating (PSI)
– Definition: PSI (pounds per square inch) measures the air pressure produced by the compressor.
– Importance: Different applications require varying pressure levels. Knowing the necessary PSI helps in selecting a compressor that can maintain consistent performance across your operations. -
Duty Cycle
– Definition: This refers to the ratio of operational time to rest time, typically expressed as a percentage.
– Importance: A higher duty cycle (over 60%) means the compressor can run continuously. This is crucial for industries requiring constant air supply, such as manufacturing and automotive sectors. -
Material Grade
– Definition: This specifies the materials used in the compressor construction, such as aluminum, cast iron, or stainless steel.
– Importance: Material quality affects durability, maintenance requirements, and operational lifespan. For heavy-duty applications, robust materials are essential to withstand high stress and wear. -
Oil-Free Technology
– Definition: Oil-free compressors use innovative designs to eliminate the need for lubrication oil.
– Importance: These compressors are crucial in industries where air purity is paramount, such as pharmaceuticals and food processing, as they prevent oil contamination.
Common Trade Terminology
-
OEM (Original Equipment Manufacturer)
– Definition: Refers to companies that produce parts and equipment that may be marketed by another manufacturer.
– Importance: Understanding OEM specifications ensures that you are sourcing high-quality, compatible components for your compressors, minimizing risks of malfunction. -
MOQ (Minimum Order Quantity)
– Definition: The smallest quantity of a product that a supplier is willing to sell.
– Importance: Knowing the MOQ helps in budgeting and inventory planning, especially for businesses looking to scale operations or for those that require large quantities of equipment. -
RFQ (Request for Quotation)
– Definition: A document that solicits pricing and other terms from suppliers for specific products or services.
– Importance: An RFQ is critical for comparing prices and terms from multiple suppliers, ensuring you receive the best deal for your investment. -
Incoterms (International Commercial Terms)
– Definition: A set of predefined international trade terms published by the International Chamber of Commerce (ICC).
– Importance: Familiarity with Incoterms helps in understanding shipping responsibilities, costs, and risks, which is essential for international buyers to avoid unexpected expenses. -
Warranty
– Definition: A guarantee provided by the manufacturer regarding the repair or replacement of a product within a specified period.
– Importance: A solid warranty can protect your investment and provide peace of mind, especially in industries where equipment failure can lead to significant operational disruptions.
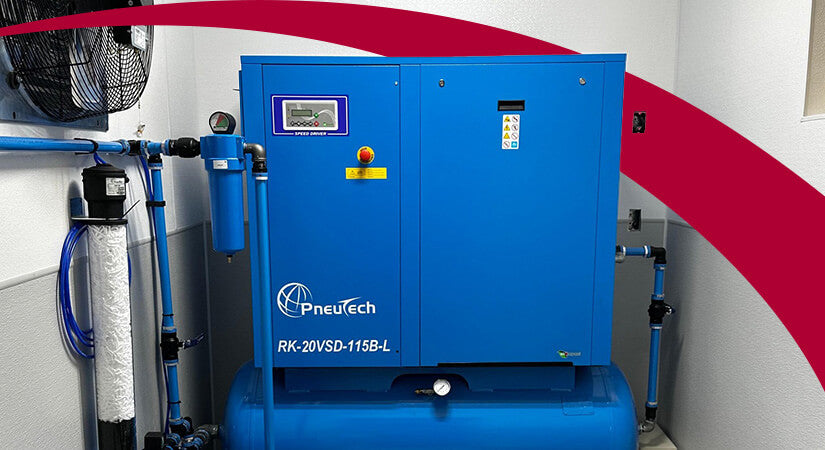
Illustrative Image (Source: Google Search)
- Maintenance Schedule
– Definition: A plan outlining routine maintenance tasks and their frequency.
– Importance: Adhering to a maintenance schedule is crucial for ensuring the longevity and reliability of your compressor, thus avoiding unexpected downtime and costly repairs.
By familiarizing yourself with these essential properties and terms, you can navigate the complexities of purchasing heavy-duty industrial air compressors, ensuring that you select the right equipment to meet your operational needs effectively.
Navigating Market Dynamics, Sourcing Trends, and Sustainability in the heavy duty industrial air compressor Sector
Market Overview & Key Trends
The heavy-duty industrial air compressor market is undergoing significant transformation, driven by technological advancements and shifting industrial demands. Key global drivers include the need for energy efficiency, increased automation, and the growing demand for compressed air in sectors like manufacturing, automotive, and construction. As industries strive to optimize operations, rotary screw compressors with variable-speed drives are becoming increasingly popular due to their efficiency and lower operational costs.
Emerging B2B sourcing trends reflect a move towards integrated solutions that not only provide compressed air but also monitor and manage energy consumption. The adoption of IoT technology allows for real-time data analysis, enabling predictive maintenance and operational efficiency, which is especially crucial for buyers in Africa, South America, the Middle East, and Europe. Furthermore, the rise of e-commerce platforms is simplifying the procurement process, making it easier for international buyers to access a diverse range of products and services.
Market dynamics are also influenced by regional factors. In Africa, the demand for reliable power sources drives interest in robust compressor systems capable of operating in challenging environments. Conversely, European markets are increasingly focused on sustainability and compliance with stringent regulations, prompting a shift towards energy-efficient and eco-friendly compressor options. This creates opportunities for international buyers to source innovative technologies that align with local market needs.
Sustainability & Ethical Sourcing in B2B
Sustainability is becoming a cornerstone of B2B procurement strategies, particularly in the heavy-duty industrial air compressor sector. The environmental impact of compressor operations, primarily due to energy consumption and emissions, necessitates a shift towards greener solutions. Buyers are increasingly seeking energy-efficient compressors that not only reduce operating costs but also minimize their carbon footprint.
The importance of ethical supply chains cannot be overstated. International buyers are now prioritizing suppliers who adhere to sustainable practices and demonstrate a commitment to reducing environmental harm. This includes sourcing materials responsibly and ensuring that manufacturing processes comply with environmental regulations. Certifications such as ISO 14001 (Environmental Management) and energy efficiency labels can serve as indicators of a supplier’s commitment to sustainability.
Moreover, the incorporation of green materials in compressor manufacturing, such as recyclable components and eco-friendly lubricants, is gaining traction. For buyers in regions like the Middle East and South America, where environmental regulations are tightening, sourcing from manufacturers with green certifications can enhance their brand reputation and compliance efforts.
Brief Evolution/History
The heavy-duty industrial air compressor sector has evolved significantly since its inception during the Industrial Revolution. Initially, air compressors were simple, mechanically operated machines used for basic tasks. Over the decades, advancements in technology have transformed them into sophisticated systems capable of delivering precise air pressure and efficiency.
The introduction of rotary screw technology in the mid-20th century marked a pivotal shift, allowing for continuous operation and higher efficiency compared to traditional reciprocating models. Today, the integration of digital technologies, such as IoT and AI, is further revolutionizing the industry, enabling predictive maintenance and operational optimization. This evolution highlights the importance of staying abreast of technological advancements for B2B buyers looking to invest in durable and efficient air compressor solutions.
Related Video: KTU S5 – Industrial Economics and Foreign Trade – Module – 1 (Part A)
Frequently Asked Questions (FAQs) for B2B Buyers of heavy duty industrial air compressor
-
What key factors should I consider when vetting suppliers for heavy duty industrial air compressors?
When vetting suppliers, prioritize their experience and reputation in the industry. Request references from previous clients and check for certifications such as ISO or CE, which indicate adherence to quality standards. Additionally, assess their financial stability and capacity to meet your order sizes. Investigate their manufacturing capabilities and whether they offer customization options to meet your specific needs. Lastly, consider their after-sales support and service, as this can significantly impact the longevity and performance of your compressor. -
Can I customize my heavy duty industrial air compressor?
Yes, many suppliers offer customization options based on your specific operational requirements. This may include modifications in size, pressure output, power source, or additional features like noise reduction technology or integrated controls. Discuss your needs with potential suppliers early in the engagement process to determine their flexibility and willingness to accommodate changes. Customization can enhance efficiency and ensure that the compressor aligns perfectly with your application. -
What are the typical minimum order quantities (MOQ) and lead times for heavy duty compressors?
Minimum order quantities can vary widely among suppliers, typically ranging from one unit for smaller manufacturers to several units for larger operations. Lead times can also differ, generally spanning from 4 to 12 weeks depending on the complexity of the order and the supplier’s current workload. It’s crucial to communicate your timeline requirements upfront to ensure the supplier can meet your deadlines, especially if you’re operating in a just-in-time manufacturing environment. -
What payment terms should I expect when purchasing heavy duty industrial air compressors?
Payment terms can vary significantly between suppliers, but it’s common to see options such as upfront payment, partial payment upon order confirmation, and final payment before shipment. Some suppliers may offer financing solutions or payment plans to ease cash flow constraints. Always clarify payment terms in advance and ensure they are documented in the purchase agreement. Additionally, consider using secure payment methods that offer buyer protection, especially when dealing with international suppliers. -
How can I ensure quality assurance and certification for my compressor?
To ensure quality assurance, request documentation of certifications such as ISO 9001, which verifies a supplier’s commitment to quality management systems. Inquire about their testing procedures and request performance guarantees. Many reputable manufacturers will provide a warranty period, which can serve as an assurance of product quality. Consider conducting a factory visit or requesting third-party inspection services to verify compliance with your quality standards before finalizing your purchase. -
What logistics considerations should I keep in mind when importing heavy duty compressors?
Importing heavy duty compressors involves several logistics considerations, including shipping methods, costs, and customs regulations. Determine whether air or sea freight is more suitable based on your urgency and budget. Ensure that the supplier can provide necessary shipping documents, such as the Bill of Lading and Certificates of Origin. Additionally, familiarize yourself with local import regulations, tariffs, and duties that may apply in your country, as these can significantly affect the total landed cost of your compressor. -
What steps should I take in case of disputes with the supplier?
In case of a dispute, begin by reviewing your contract to understand the terms and conditions related to dispute resolution. Most contracts will include a clause for mediation or arbitration, which can be a more amicable way to resolve issues than litigation. Maintain clear and documented communication with the supplier throughout the process, as this can help clarify misunderstandings. If the issue cannot be resolved directly, consider seeking legal advice or involving a third-party mediator to help facilitate a resolution. -
How do I handle maintenance and support after purchasing my compressor?
After purchasing, establish a maintenance schedule based on the manufacturer’s recommendations to ensure optimal performance. Request training from the supplier for your team on proper operation and troubleshooting. Many suppliers offer maintenance contracts or service packages, which can be beneficial for ongoing support. Keep records of all maintenance activities and inspections, as these can help in identifying potential issues early and maintaining warranty coverage. Additionally, establish a point of contact with the supplier for any technical support you may need in the future.
Important Disclaimer & Terms of Use
⚠️ Important Disclaimer
The information provided in this guide, including content regarding manufacturers, technical specifications, and market analysis, is for informational and educational purposes only. It does not constitute professional procurement advice, financial advice, or legal advice.
While we have made every effort to ensure the accuracy and timeliness of the information, we are not responsible for any errors, omissions, or outdated information. Market conditions, company details, and technical standards are subject to change.
B2B buyers must conduct their own independent and thorough due diligence before making any purchasing decisions. This includes contacting suppliers directly, verifying certifications, requesting samples, and seeking professional consultation. The risk of relying on any information in this guide is borne solely by the reader.
Strategic Sourcing Conclusion and Outlook for heavy duty industrial air compressor
The strategic sourcing of heavy-duty industrial air compressors is pivotal for optimizing operational efficiency and ensuring long-term profitability. By carefully evaluating the types of compressors—such as reciprocating, rotary screw, and oil-free scroll—international buyers can align their choices with specific operational needs. Key considerations include understanding air demand, energy efficiency, and potential growth requirements.
Investing in quality compressors not only enhances productivity but also reduces maintenance costs and downtime. It is essential for businesses in Africa, South America, the Middle East, and Europe to engage with suppliers who offer comprehensive support and tailored solutions.
Looking ahead, the demand for innovative and efficient air compressor technologies is set to grow, driven by increased industrial activity and a focus on sustainability. B2B buyers are encouraged to leverage this trend by sourcing strategically, ensuring they remain competitive in a rapidly evolving market. Embrace the opportunity to invest in cutting-edge solutions that will propel your business forward and meet the challenges of tomorrow.