Your Ultimate Guide to Sourcing Industrial Air Compressor
Introduction: Navigating the Global Market for industrial air compressor 60 gallon
The industrial air compressor, particularly the 60-gallon variant, is a cornerstone of modern manufacturing and construction operations worldwide. Its ability to deliver substantial air pressure and volume makes it indispensable for powering tools, machinery, and equipment in various sectors. For international B2B buyers, especially those operating in Africa, South America, the Middle East, and Europe—regions characterized by diverse industrial needs and emerging markets—understanding the nuances of selecting the right compressor can significantly enhance operational efficiency and productivity.
This guide offers a comprehensive overview of the industrial air compressor landscape, focusing specifically on the 60-gallon models. It covers essential topics such as types of compressors, materials used in construction, manufacturing and quality control practices, supplier selection, and cost considerations. Additionally, it addresses common FAQs to clarify any uncertainties that may arise during the procurement process.
By leveraging the insights presented in this guide, B2B buyers can make informed sourcing decisions that align with their operational requirements and budget constraints. Whether you’re looking to upgrade existing equipment or invest in new technology, understanding the market dynamics and product specifications is crucial for maximizing your return on investment and ensuring seamless integration into your operations. With the right knowledge, you can navigate the complexities of the global market and secure the best solutions for your industrial needs.
Understanding industrial air compressor 60 gallon Types and Variations
Type Name | Key Distinguishing Features | Primary B2B Applications | Brief Pros & Cons for Buyers |
---|---|---|---|
Rotary Screw Compressor | Continuous operation, high efficiency, low maintenance | Manufacturing, automotive, food processing | Pros: Efficient for continuous use; Cons: Higher initial cost. |
Reciprocating Air Compressor | Piston-driven, variable pressure output, compact size | Construction, automotive repair, woodworking | Pros: Cost-effective; Cons: Noisy operation and more maintenance. |
Two-Stage Air Compressor | Higher pressure capability, two compression stages | Heavy-duty applications, industrial machinery | Pros: Greater efficiency at high pressures; Cons: Larger footprint. |
Oil-Free Air Compressor | No oil contamination, low maintenance | Food and beverage, pharmaceuticals, electronics | Pros: Ensures clean air; Cons: Generally lower durability. |
Portable Air Compressor | Lightweight, easy to transport, versatile | Construction sites, outdoor applications | Pros: Convenient for mobile use; Cons: Limited power and capacity. |
Rotary Screw Compressor
Rotary screw compressors are known for their ability to deliver a continuous flow of compressed air, making them ideal for industrial applications that require a steady supply. These compressors use two helical screws to compress air, resulting in efficient and reliable performance. They are suitable for manufacturing, automotive, and food processing industries where high efficiency and low maintenance are critical. When considering a rotary screw compressor, buyers should evaluate their operational needs, as the initial investment can be higher compared to other types.
Reciprocating Air Compressor
Reciprocating air compressors utilize a piston-driven mechanism to compress air, making them versatile for various applications, including construction and automotive repair. They are often more affordable than other compressor types, which appeals to budget-conscious buyers. However, they can be noisier and require more maintenance due to their mechanical components. B2B buyers should consider the frequency of use and whether noise levels will impact their working environment.
Two-Stage Air Compressor
Two-stage air compressors are designed for heavy-duty applications, providing higher pressure capabilities through two compression stages. This makes them suitable for industrial machinery and demanding tasks that require consistent high pressure. The efficiency of two-stage compressors at elevated pressures can lead to reduced energy costs over time. Buyers should consider the space requirements, as these compressors tend to have a larger footprint, which may impact installation in smaller facilities.
Oil-Free Air Compressor
Oil-free air compressors are essential in industries where air purity is paramount, such as food and beverage, pharmaceuticals, and electronics. They eliminate the risk of oil contamination, ensuring that the compressed air is clean and suitable for sensitive applications. While these compressors offer significant benefits in terms of air quality, they may be less durable than oil-lubricated models. B2B buyers should assess their specific air quality requirements and balance them against the potential longevity of the equipment.
Portable Air Compressor
Portable air compressors are lightweight and designed for easy transportation, making them ideal for construction sites and outdoor applications. Their versatility allows them to power various tools, although they may have limitations in terms of power and capacity compared to stationary models. Buyers should consider the balance between portability and the operational demands of their tasks to ensure they select a model that meets their needs without sacrificing performance.
Related Video: 60-Gallon Air Compressor Setup and Shop Air Installation Industrial Air (Setup Part One)
Key Industrial Applications of industrial air compressor 60 gallon
Industry/Sector | Specific Application of industrial air compressor 60 gallon | Value/Benefit for the Business | Key Sourcing Considerations for this Application |
---|---|---|---|
Manufacturing | Powering pneumatic tools for assembly lines | Increases efficiency and reduces manual labor costs | Reliability and durability of the compressor system |
Automotive Repair | Spray painting and bodywork | Provides consistent pressure for quality finishes | Air purity and filtration systems to avoid contaminants |
Construction | Operating pneumatic hammers and nail guns | Enhances productivity and speeds up project timelines | Portability and ease of use in various job sites |
Food & Beverage | Blowing and filling operations in packaging | Ensures efficient production and reduces waste | Compliance with food safety standards |
Textile Industry | Air jet weaving machines | Improves fabric quality and production rates | Energy efficiency and maintenance support |
Manufacturing
In the manufacturing sector, a 60-gallon industrial air compressor is crucial for powering pneumatic tools used in assembly lines. This includes air drills, impact wrenches, and riveters, which require a consistent and reliable air supply. By utilizing such compressors, manufacturers can significantly boost efficiency, reduce manual labor, and maintain high production rates. For international buyers, particularly from Africa and South America, sourcing compressors that offer robust performance and energy efficiency is paramount, as operational costs can directly affect profit margins.
Automotive Repair
The automotive repair industry relies heavily on 60-gallon air compressors for spray painting and bodywork applications. These compressors provide the necessary air pressure for spray guns, ensuring even application and high-quality finishes. The ability to operate multiple tools simultaneously is a significant advantage, allowing for increased productivity. Buyers in Europe and the Middle East should focus on compressors with advanced filtration systems to maintain air purity, thus preventing paint defects caused by contaminants.
Construction
In construction, a 60-gallon air compressor is often used to power pneumatic hammers, nail guns, and other heavy-duty tools. This application accelerates project timelines by enhancing productivity and reducing the physical strain on workers. For buyers in regions with diverse job sites, such as Africa and South America, selecting a compressor that is both portable and easy to use is essential. Additionally, durability and weather resistance are critical factors to consider, given the harsh conditions often encountered on construction sites.
Food & Beverage
In the food and beverage industry, 60-gallon air compressors are employed for blowing and filling operations in packaging processes. The consistent air supply ensures efficient production lines and minimizes waste, which is vital for maintaining profitability. International buyers must ensure that the compressors sourced comply with stringent food safety standards, particularly in regions like Europe, where regulations are strict. Investing in compressors with effective air filtration systems can help meet these standards and improve overall operational efficiency.
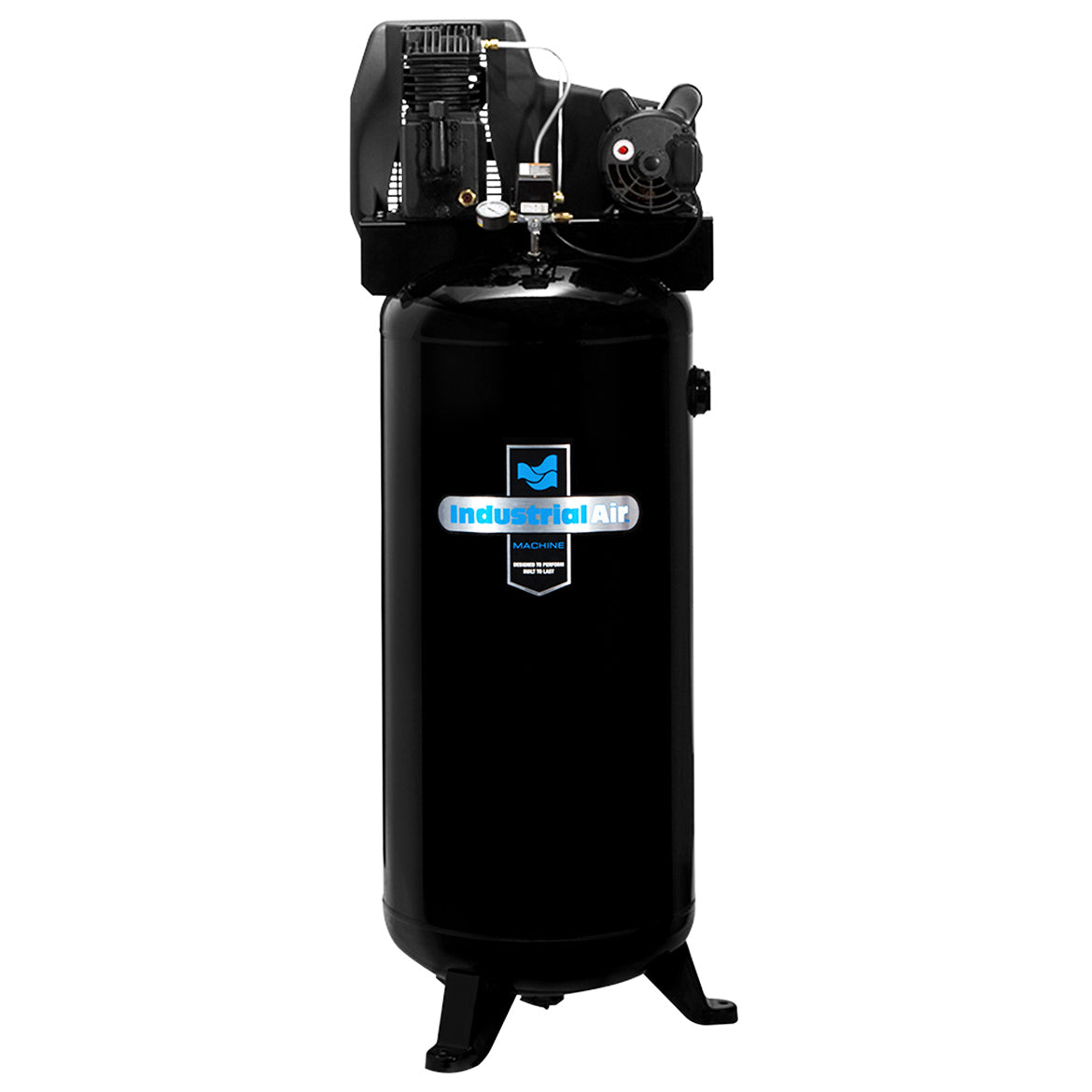
Illustrative Image (Source: Google Search)
Textile Industry
The textile industry utilizes 60-gallon air compressors primarily in air jet weaving machines. These compressors supply the necessary air pressure to operate the machines effectively, leading to improved fabric quality and higher production rates. For B2B buyers in South America and Africa, energy efficiency and ease of maintenance are significant considerations when sourcing compressors, as these factors can influence long-term operational costs and sustainability practices within the industry.
Strategic Material Selection Guide for industrial air compressor 60 gallon
When selecting materials for a 60-gallon industrial air compressor, it’s essential to consider the properties, advantages, and limitations of various materials. This selection directly impacts performance, durability, and operational efficiency. Below, we analyze four common materials used in the construction of industrial air compressors, focusing on their suitability for international B2B buyers.
1. Steel
Key Properties:
Steel is known for its high tensile strength and excellent pressure resistance, making it suitable for high-pressure applications. It can withstand temperatures up to 400°F (204°C) and is often coated to enhance corrosion resistance.
Pros & Cons:
Steel is durable and can handle significant wear and tear, which is vital for industrial applications. However, it is heavier than other materials, which can increase shipping costs. The manufacturing complexity is moderate, as steel requires welding and machining.
Impact on Application:
Steel is compatible with various media, including air and gas. However, its susceptibility to rust and corrosion in humid environments necessitates protective coatings, particularly in regions with high moisture levels.
Considerations for International Buyers:
Compliance with standards such as ASTM A36 is crucial. Buyers from regions like Europe may prefer galvanized steel for enhanced corrosion resistance, while those in Africa and South America should consider local environmental conditions.
2. Aluminum
Key Properties:
Aluminum is lightweight and has a good strength-to-weight ratio. It can handle pressures up to 150 psi and is resistant to corrosion due to its natural oxide layer.
Pros & Cons:
Aluminum is easy to fabricate, reducing manufacturing complexity. Its lightweight nature lowers shipping costs, but it is less durable than steel and can deform under high pressure or impact.
Impact on Application:
Aluminum is suitable for applications requiring lightweight components, such as portable compressors. However, its lower pressure rating limits its use in heavy-duty industrial applications.
Considerations for International Buyers:
Compliance with standards such as ASTM B221 is important. Buyers in Europe may prefer aluminum for its lightweight properties, while those in the Middle East might need to consider heat resistance in high-temperature environments.
3. Cast Iron
Key Properties:
Cast iron offers excellent wear resistance and can withstand high pressures, typically up to 175 psi. It performs well at elevated temperatures, making it suitable for industrial applications.
Pros & Cons:
The durability of cast iron is a significant advantage, as it can last for decades with proper maintenance. However, it is heavy and brittle, making it more challenging to transport and install.
Impact on Application:
Cast iron is ideal for stationary compressors used in heavy-duty applications. Its ability to absorb vibrations makes it suitable for noise-sensitive environments.
Considerations for International Buyers:
Compliance with standards like ASTM A48 is essential. Buyers in South America and Africa should consider local availability and the cost implications of transporting heavy materials.
4. Composite Materials
Key Properties:
Composite materials can include fiberglass and reinforced polymers, offering excellent corrosion resistance and lightweight properties. They can handle moderate pressures, typically around 100 psi.
Pros & Cons:
The primary advantage of composites is their resistance to corrosion and chemical damage, making them suitable for harsh environments. However, they can be more expensive than traditional materials and may have limitations in high-pressure applications.
Impact on Application:
Composites are ideal for applications where weight reduction and corrosion resistance are critical, such as in mobile or offshore compressors.
Considerations for International Buyers:
Buyers should ensure compliance with relevant standards, such as ASTM D638 for plastics. In regions like Europe, where environmental regulations are stringent, composites may be favored for their longevity and reduced maintenance.
Summary Table
Material | Typical Use Case for industrial air compressor 60 gallon | Key Advantage | Key Disadvantage/Limitation | Relative Cost (Low/Med/High) |
---|---|---|---|---|
Steel | Heavy-duty industrial applications | High strength and durability | Heavier, higher shipping costs | Medium |
Aluminum | Portable compressors | Lightweight and easy to fabricate | Lower pressure rating | Medium |
Cast Iron | Stationary compressors | Excellent wear resistance | Heavy and brittle | High |
Composite Materials | Mobile or offshore compressors | Corrosion resistance | Higher cost and pressure limits | High |
This analysis provides a comprehensive overview of material options for a 60-gallon industrial air compressor, helping international B2B buyers make informed decisions based on their specific needs and regional conditions.
In-depth Look: Manufacturing Processes and Quality Assurance for industrial air compressor 60 gallon
Manufacturing Processes for Industrial Air Compressors
The manufacturing of a 60-gallon industrial air compressor involves several critical stages, each designed to ensure functionality, reliability, and efficiency. Understanding these processes can help B2B buyers make informed decisions when sourcing compressors for their operations.
Material Preparation
The first step in manufacturing involves the selection and preparation of materials. Common materials used include:
- Steel: High-quality steel is often used for the compressor tank due to its strength and ability to withstand high pressure.
- Aluminum: Lightweight and resistant to corrosion, aluminum is typically used for components like the compressor head.
- Copper: Used for piping and electrical components, copper offers excellent conductivity and durability.
Materials undergo rigorous inspection to ensure they meet specific standards. This includes checking for impurities, thickness, and tensile strength, ensuring they can handle the operational demands of a compressor.
Forming
In the forming stage, raw materials are shaped into components using various techniques:
- Stamping: This process shapes metal sheets into specific forms, which are then used for the compressor casing and other parts.
- Machining: Precision machining techniques, such as CNC (Computer Numerical Control) milling and turning, are employed to create intricate parts like the rotors and valves.
- Welding: Essential for joining different components, welding ensures that the tank and other parts are sealed and can withstand high pressure.
Each method is chosen based on the design requirements and the specific characteristics of the materials used.
Assembly
The assembly process involves bringing together all the manufactured components. Key steps include:
- Sub-Assembly: Individual components, such as the motor, pump, and tank, are assembled separately before the final assembly.
- Final Assembly: The sub-assemblies are then combined, and all necessary connections (air, electrical, and mechanical) are made.
- Installation of Safety Features: Safety valves, pressure gauges, and emergency shut-off systems are installed to comply with safety regulations.
Attention to detail during assembly is crucial, as it directly affects the performance and longevity of the compressor.
Finishing
The finishing stage enhances both the aesthetics and durability of the air compressor. Common processes include:
- Painting: High-quality, industrial-grade paint is applied to prevent corrosion and enhance appearance.
- Surface Treatment: Techniques like powder coating or anodizing are used to improve surface hardness and resistance to wear.
- Quality Control Checks: Each finished unit undergoes a series of inspections to ensure that it meets specifications and is free from defects.
Quality Assurance Standards
Quality assurance (QA) is a critical aspect of manufacturing air compressors. International standards and industry-specific certifications help ensure that the compressors meet safety, reliability, and performance criteria.
International Standards
- ISO 9001: This standard focuses on quality management systems and is essential for manufacturers to demonstrate their commitment to quality processes.
- CE Marking: Indicates compliance with European health, safety, and environmental protection standards. For buyers in Europe, this certification is crucial.
- API Standards: The American Petroleum Institute sets standards for equipment used in the oil and natural gas industry, which can also apply to compressors used in these sectors.
Quality Control Checkpoints
To maintain high standards, manufacturers implement various quality control checkpoints throughout the production process:
- Incoming Quality Control (IQC): Materials are inspected upon arrival to ensure they meet required specifications.
- In-Process Quality Control (IPQC): Ongoing inspections during the manufacturing process help identify and rectify defects early.
- Final Quality Control (FQC): The finished compressors undergo rigorous testing to verify performance, safety, and compliance with standards.
Common Testing Methods
Manufacturers typically employ several testing methods to ensure the compressors function correctly:
- Pressure Testing: Checks the integrity of the tank and components under high pressure.
- Leak Testing: Ensures that there are no air leaks in the system, which could lead to inefficiencies.
- Performance Testing: Evaluates the compressor’s output against specified CFM (cubic feet per minute) and PSI (pounds per square inch) ratings.
Verifying Supplier Quality Control
For international B2B buyers, verifying a supplier’s quality control processes is crucial to ensure the reliability of the products being sourced.
Audits and Reports
- Supplier Audits: Conducting audits helps buyers assess the manufacturing processes, quality control measures, and compliance with international standards.
- Quality Reports: Requesting detailed quality reports from suppliers can provide insights into their testing methodologies and results.
Third-Party Inspections
Engaging third-party inspection services can add an additional layer of assurance. These services can conduct independent assessments of the manufacturing processes and the final products, ensuring compliance with quality standards.
Quality Control Nuances for International Buyers
When sourcing industrial air compressors, particularly from regions such as Africa, South America, the Middle East, and Europe, buyers should be aware of specific nuances:
- Regulatory Compliance: Different regions may have varying regulations regarding safety and performance standards. Buyers should ensure that the products comply with local regulations in their respective countries.
- Cultural Considerations: Understanding cultural differences in communication and business practices can facilitate smoother negotiations and partnerships with suppliers.
- Logistics and Supply Chain: Consideration of shipping and logistics is crucial, as delays can impact the supply chain. Establishing clear communication with suppliers about delivery timelines and expectations is essential.
In conclusion, understanding the manufacturing processes and quality assurance standards for industrial air compressors is vital for B2B buyers. By focusing on these aspects, buyers can make informed decisions, ensuring they invest in reliable, high-quality equipment that meets their operational needs.
Comprehensive Cost and Pricing Analysis for industrial air compressor 60 gallon Sourcing
When sourcing a 60-gallon industrial air compressor, understanding the cost structure and pricing dynamics is crucial for international B2B buyers. This analysis covers the essential cost components, price influencers, and practical buyer tips to facilitate informed purchasing decisions.
Cost Components
-
Materials: The primary components of a 60-gallon air compressor include the tank, motor, pump, and various fittings. The choice between steel and aluminum for the tank can significantly affect costs, with steel typically being less expensive but heavier. Additionally, quality components such as high-grade seals and valves can increase durability but also the price.
-
Labor: Labor costs are influenced by the manufacturing location. Regions with lower labor costs, such as parts of South America and Asia, may offer more competitive pricing compared to European manufacturers. However, labor skill levels can vary, impacting the quality of the final product.
-
Manufacturing Overhead: This includes factory costs such as utilities, rent, and administrative expenses. Companies with advanced manufacturing processes may have higher overhead but can also offer enhanced quality and reliability.
-
Tooling: Initial tooling costs for manufacturing specific designs can be significant. Customizations or specialized features will require additional investment in tooling, which may be passed on to the buyer.
-
Quality Control (QC): Comprehensive QC processes ensure that compressors meet industry standards. Suppliers that invest in stringent QC measures may have higher pricing but offer better reliability and lower failure rates.
-
Logistics: Shipping and handling costs can vary dramatically based on the supplier’s location and the buyer’s destination. International shipping, tariffs, and customs duties can significantly influence the final cost.
-
Margin: The manufacturer’s profit margin can vary based on brand reputation, market competition, and the perceived value of the product. Established brands may command higher prices due to their reliability and service support.
Price Influencers
-
Volume/MOQ: Buyers can often negotiate better pricing based on order volume. Higher minimum order quantities (MOQs) may unlock bulk pricing discounts.
-
Specs/Customization: Tailoring the compressor to specific needs (like pressure ratings or additional features) can increase costs. Buyers should weigh the benefits of customization against the additional expenses.
-
Materials: The choice of materials directly impacts pricing. Oil-free compressors, for example, are typically more expensive due to the technology involved.
-
Quality/Certifications: Products with certifications (e.g., ISO, CE) may have higher prices but offer assurance of quality. This is particularly vital for buyers in regions with stringent regulatory requirements.
-
Supplier Factors: Supplier reputation, service quality, and warranty offerings can influence prices. Established suppliers may charge a premium but provide better support and reliability.
-
Incoterms: Understanding Incoterms (International Commercial Terms) is essential for international buyers, as they define responsibilities for shipping costs, insurance, and liability. Choosing the right Incoterm can help manage overall costs effectively.
Buyer Tips
-
Negotiation: Always negotiate terms and pricing. Leverage volume purchasing or long-term relationships for better deals.
-
Cost-Efficiency: Consider the total cost of ownership (TCO), which includes maintenance, energy consumption, and potential downtime costs. A slightly higher upfront cost may be justified by lower operational costs over the compressor’s lifespan.
-
Pricing Nuances: Be aware of currency fluctuations and economic conditions in the supplier’s country. These factors can affect pricing stability and should be factored into budget planning.
-
Regional Considerations: For buyers in Africa, South America, the Middle East, and Europe, understanding local market conditions and supplier capabilities is crucial. Engage with local distributors to navigate import regulations and logistics challenges effectively.
Disclaimer
Prices for industrial air compressors can vary widely based on the factors mentioned above. The insights provided here are indicative and should be confirmed with suppliers for the most accurate and current pricing information.
Essential Technical Properties and Trade Terminology for industrial air compressor 60 gallon
Key Technical Properties of a 60 Gallon Industrial Air Compressor
When considering a 60-gallon industrial air compressor, several technical specifications are vital for ensuring optimal performance and suitability for specific applications. Here are some essential properties:
-
Horsepower (HP)
Horsepower indicates the power output of the compressor’s motor. A typical range for a 60-gallon compressor is between 3 to 5 HP. Higher horsepower ratings allow the compressor to deliver more air pressure and volume, crucial for heavy-duty applications. For B2B buyers, selecting the right horsepower can significantly impact efficiency and energy consumption. -
Cubic Feet per Minute (CFM)
CFM measures the volume of air the compressor can deliver at a specific pressure, usually at 90 PSI. A 60-gallon compressor typically provides a CFM range from 10 to 15. Understanding CFM is essential for matching the compressor to the tools and equipment that will be used, ensuring that they receive adequate air supply for optimal operation. -
Pressure Rating (PSI)
The pressure rating, measured in pounds per square inch (PSI), indicates the maximum pressure the compressor can generate. Most 60-gallon compressors operate between 120 to 175 PSI. This specification is critical for B2B buyers to assess whether the compressor can meet the pressure requirements of specific applications, such as spray painting or pneumatic tool operation. -
Tank Material
The material of the tank is typically steel or aluminum. Steel tanks are more durable and can withstand higher pressures, while aluminum tanks are lighter and resistant to rust. Understanding tank material is vital for buyers, as it affects longevity, portability, and maintenance considerations. -
Stage Configuration
Compressors can be either single-stage or two-stage. A single-stage compressor compresses air in one stroke, while a two-stage compressor compresses air twice, resulting in higher efficiency and pressure. For B2B applications requiring consistent and high-pressure output, two-stage compressors are often preferred. -
Noise Level (dB)
Noise level, measured in decibels (dB), is an important consideration for workplace comfort. A typical 60-gallon compressor can range from 70 to 90 dB. B2B buyers should consider noise levels, especially for indoor operations, to ensure compliance with workplace regulations and to maintain a conducive working environment.
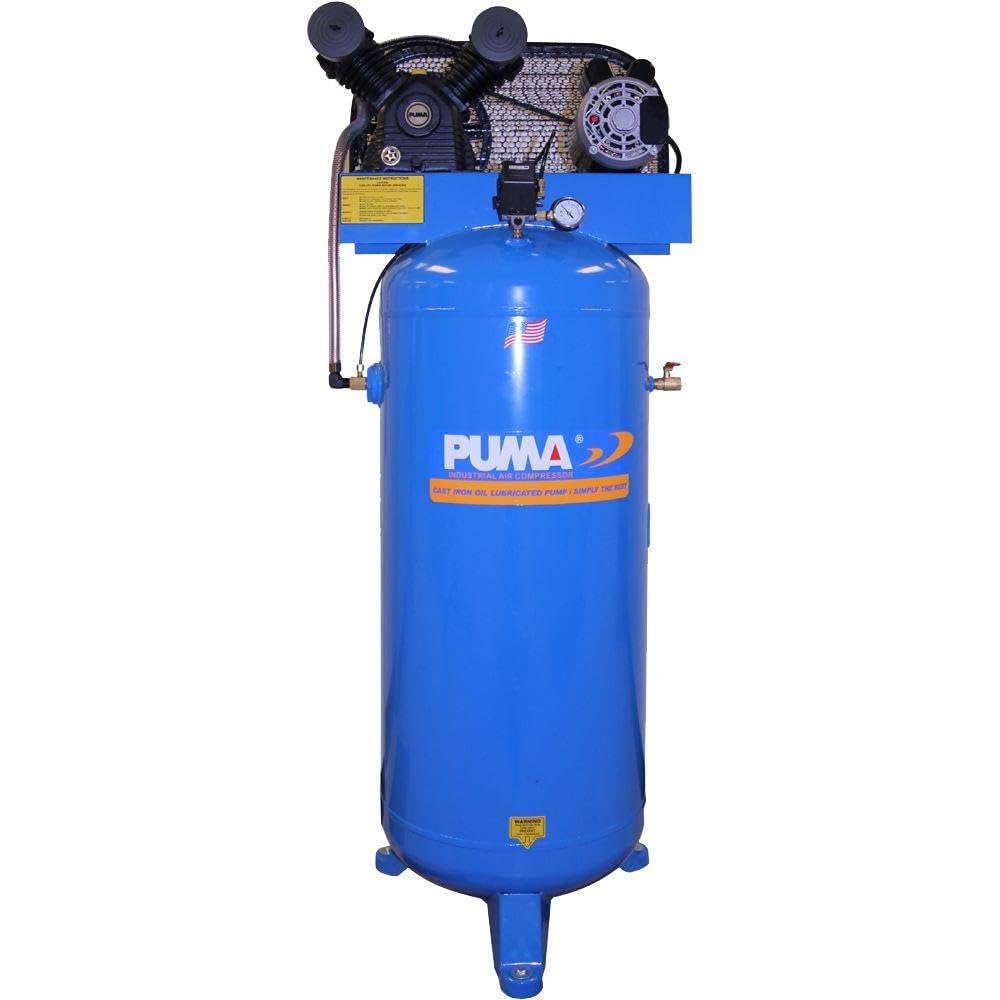
Illustrative Image (Source: Google Search)
Common Trade Terminology
Understanding industry jargon is crucial for effective communication and negotiation in B2B transactions. Here are some common terms relevant to industrial air compressors:
-
OEM (Original Equipment Manufacturer)
An OEM refers to the company that produces the components or products that are sold under another company’s brand. In the air compressor industry, buyers should verify if the compressor is sourced from a reputable OEM to ensure quality and reliability. -
MOQ (Minimum Order Quantity)
MOQ denotes the smallest quantity of a product that a supplier is willing to sell. For B2B buyers, understanding MOQ is essential for budgeting and inventory management, particularly when sourcing compressors or replacement parts in bulk. -
RFQ (Request for Quotation)
An RFQ is a document sent to suppliers requesting pricing information for specific products or services. B2B buyers should prepare RFQs that detail their needs for compressors, including specifications and quantities, to obtain accurate pricing and terms. -
Incoterms (International Commercial Terms)
Incoterms are international trade terms that define the responsibilities of buyers and sellers regarding shipping, insurance, and tariffs. Familiarity with Incoterms is crucial for B2B buyers when negotiating shipping arrangements for compressors across borders. -
Service Intervals
This term refers to the scheduled maintenance periods for the air compressor. Understanding service intervals helps B2B buyers plan maintenance to ensure longevity and reliability, minimizing downtime in industrial operations. -
Warranty Period
The warranty period indicates the duration that the manufacturer covers defects in materials and workmanship. B2B buyers should consider warranty terms when purchasing compressors, as this can be an indicator of the manufacturer’s confidence in their product’s quality.
By grasping these technical properties and trade terminologies, B2B buyers can make informed decisions, ensuring they select the right 60-gallon air compressor for their industrial needs.
Navigating Market Dynamics, Sourcing Trends, and Sustainability in the industrial air compressor 60 gallon Sector
Market Overview & Key Trends
The industrial air compressor market, particularly for 60-gallon units, is experiencing robust growth driven by several global factors. The increasing demand for compressed air across diverse industries, such as manufacturing, automotive, and construction, is a primary market driver. As industrial operations become more automated and efficiency-focused, the need for reliable air compressors that can support pneumatic tools and machinery is paramount.
Emerging trends include the integration of smart technologies and IoT capabilities in air compressors, allowing for real-time monitoring and predictive maintenance. This shift not only enhances operational efficiency but also reduces downtime—a crucial aspect for international buyers looking to optimize production costs. Additionally, the growing emphasis on energy efficiency is prompting manufacturers to develop compressors that consume less power while delivering higher performance.
For international B2B buyers, particularly from Africa, South America, the Middle East, and Europe, understanding local market dynamics is essential. In regions like Africa and South America, infrastructure improvements and industrialization efforts are boosting the demand for reliable compressed air systems. Meanwhile, European markets are leaning towards advanced, energy-efficient technologies that align with stringent environmental regulations. Buyers should focus on suppliers who can offer tailored solutions that meet both local compliance standards and operational needs.
Sustainability & Ethical Sourcing in B2B
Sustainability is increasingly influencing purchasing decisions in the industrial air compressor sector. The environmental impact of air compressors, particularly in terms of energy consumption and emissions, is a critical consideration for B2B buyers. Compressors that utilize energy-efficient technologies not only lower operational costs but also contribute to reducing the carbon footprint of industrial activities.
Ethical sourcing is also becoming vital as companies seek to build responsible supply chains. Buyers should prioritize manufacturers who demonstrate transparency in their sourcing practices and adhere to ethical labor standards. Furthermore, certifications such as ISO 14001 (Environmental Management) and energy efficiency labels can serve as indicators of a manufacturer’s commitment to sustainability.
Investing in compressors made from recyclable materials or those that have a lower environmental impact during their lifecycle is advantageous. This not only meets the growing demand for sustainable solutions but also aligns with global trends toward responsible consumption. Buyers from regions like Europe, where sustainability is heavily emphasized, should consider these factors when selecting suppliers.
Brief Evolution/History
The evolution of industrial air compressors dates back to the late 19th century, when the first reciprocating compressors were developed for use in various industries. Initially, these machines were simple and inefficient, primarily used for powering pneumatic tools. As industrial demands increased, technological advancements led to the introduction of rotary screw compressors in the mid-20th century, which offered higher efficiency and reliability.
Today, the 60-gallon air compressor stands as a versatile solution suitable for a wide range of applications, from heavy-duty industrial tasks to small-scale workshops. Modern compressors are equipped with advanced features such as variable speed drives and smart technology, reflecting the ongoing trend towards automation and energy efficiency. This historical context is crucial for B2B buyers, as it highlights the continuous innovation and adaptation of air compressor technology to meet evolving market needs.
Related Video: Top 5 Best 60 Gallon Air Compressors Review in 2024
Frequently Asked Questions (FAQs) for B2B Buyers of industrial air compressor 60 gallon
-
What should I consider when vetting suppliers for a 60-gallon industrial air compressor?
When vetting suppliers, assess their industry experience, reputation, and customer feedback. Verify certifications such as ISO 9001 or CE marking, which indicate compliance with international quality standards. Request references from existing clients to gauge reliability and service quality. Additionally, inquire about their manufacturing capabilities, warranty policies, and after-sales support to ensure they can meet your specific needs. -
Can I customize my 60-gallon air compressor to suit my operational requirements?
Yes, many suppliers offer customization options for their air compressors. You can request specific features such as pressure settings, motor size, or tank materials to align with your operational needs. Discuss your requirements upfront to determine if the supplier can accommodate them. Keep in mind that extensive customization may affect lead times and pricing, so clarify these aspects during negotiations. -
What is the typical minimum order quantity (MOQ) for a 60-gallon air compressor, and how do lead times vary?
MOQs can vary widely depending on the supplier and their production capacity. Some suppliers may offer single-unit purchases, while others might require a MOQ of 5-10 units. Lead times can also differ based on customization requests and shipping logistics. Typically, expect lead times of 4-12 weeks. It’s crucial to confirm these details during the initial discussions to ensure they align with your project timelines. -
What payment options are commonly accepted for purchasing industrial air compressors?
Most suppliers accept various payment methods, including bank transfers, letters of credit, and PayPal. It’s essential to clarify payment terms upfront, including any deposit requirements and payment schedules. Ensure that you understand the currency in which payments are accepted, as this can impact international transactions. Establishing a secure payment method is critical to mitigate risks in international trade. -
What quality assurance measures should I look for when sourcing a 60-gallon air compressor?
Look for suppliers that adhere to rigorous quality control processes, such as ISO certifications or third-party inspections. Request documentation detailing their QA procedures, including testing protocols for performance and safety. Ensure the compressor meets your country’s regulatory standards, which may include certifications like CE marking for Europe or UL certification for North America. This will help ensure the reliability and safety of the equipment. -
How should I manage logistics when importing a 60-gallon air compressor?
Logistics planning is vital when importing heavy equipment like air compressors. Engage a reliable freight forwarder experienced in handling industrial machinery to navigate customs and transportation. Discuss shipping options, including sea or air freight, and evaluate costs versus delivery times. Additionally, ensure that the supplier provides all necessary documentation for customs clearance, including invoices, packing lists, and certificates of origin. -
What steps can I take to resolve disputes with suppliers?
Establish clear communication channels and maintain documentation of all agreements and transactions to mitigate disputes. If issues arise, start by addressing concerns directly with the supplier to seek a resolution. If necessary, refer to your contract’s dispute resolution clause, which may outline mediation or arbitration processes. Engaging legal counsel familiar with international trade laws can also provide guidance on navigating complex disputes. -
What are the common certifications to look for in a 60-gallon air compressor?
Key certifications to consider include ISO 9001 for quality management systems and ISO 14001 for environmental management. In regions like Europe, CE marking indicates compliance with health, safety, and environmental protection standards. Additionally, check for UL certification for safety in North America. These certifications not only assure product quality but also enhance credibility in international markets, making it essential to verify them during supplier evaluation.
Important Disclaimer & Terms of Use
⚠️ Important Disclaimer
The information provided in this guide, including content regarding manufacturers, technical specifications, and market analysis, is for informational and educational purposes only. It does not constitute professional procurement advice, financial advice, or legal advice.
While we have made every effort to ensure the accuracy and timeliness of the information, we are not responsible for any errors, omissions, or outdated information. Market conditions, company details, and technical standards are subject to change.
B2B buyers must conduct their own independent and thorough due diligence before making any purchasing decisions. This includes contacting suppliers directly, verifying certifications, requesting samples, and seeking professional consultation. The risk of relying on any information in this guide is borne solely by the reader.
Strategic Sourcing Conclusion and Outlook for industrial air compressor 60 gallon
In conclusion, the strategic sourcing of a 60-gallon industrial air compressor is essential for maximizing operational efficiency and cost-effectiveness. As highlighted, understanding the specific requirements of your applications—from pneumatic tool usage to material handling—is crucial in selecting the right compressor type, whether it be rotary screw or reciprocating.
Key Takeaways:
– Assessment of Needs: Clearly define your operational needs to ensure the selected compressor meets your pressure and capacity requirements.
– Cost Considerations: Evaluate the total cost of ownership, including maintenance and energy consumption, to make an informed investment.
– Supplier Relationships: Build strong relationships with reliable suppliers to gain access to quality products and support services.
As international B2B buyers from Africa, South America, the Middle East, and Europe navigate this vital equipment procurement, it’s important to leverage local insights and global best practices. The future of industrial air compressors lies in their adaptability to evolving technologies and sustainability standards.
Call to Action: Engage with trusted vendors, attend industry expos, and participate in forums to stay abreast of innovations in compressed air technology. Make informed decisions that not only enhance productivity but also contribute to a sustainable industrial environment.