Your Ultimate Guide to Sourcing Laser Cnc Machine For Metal
Introduction: Navigating the Global Market for laser cnc machine for metal
In the competitive realm of global manufacturing, laser CNC machines for metal stand as transformative tools that significantly enhance production precision and efficiency. For B2B buyers across diverse regions—including Africa, South America, the Middle East, and Europe—understanding the critical role these machines play is essential for leveraging opportunities and optimizing operations. Whether you’re in bustling Lagos, innovative São Paulo, or the industrial hubs of Milan and Dubai, the right laser CNC solution can elevate your manufacturing capabilities, ensuring you stay ahead of the curve.
This guide offers a comprehensive exploration of laser CNC technology, detailing various machine types, their compatibility with different materials, and essential manufacturing and quality control processes. We delve into the intricacies of sourcing from reputable suppliers, dissecting cost structures and market trends, while equipping buyers with effective negotiation tactics. By addressing frequently asked questions, we aim to demystify the complexities of laser CNC machines, empowering you to make informed sourcing decisions.
With actionable insights tailored for international B2B buyers, this guide serves as a vital resource for navigating the global market. By harnessing the knowledge contained herein, businesses can streamline procurement processes, reduce risks, and foster sustainable growth in today’s dynamic manufacturing landscape. Embrace the future of metalworking with confidence and position your enterprise for success on the international stage.
Understanding laser cnc machine for metal Types and Variations
Type Name | Key Distinguishing Features | Primary B2B Applications | Brief Pros & Cons for Buyers |
---|---|---|---|
Fiber Laser CNC Cutting Machine | Solid-state laser with fiber optics; high efficiency | Sheet metal, automotive, electronics | Pros: Fast, energy-efficient, low maintenance; Cons: Higher upfront cost, best for metals |
CO₂ Laser CNC Cutting Machine | Gas-based laser suitable for non-metals and thin metals | Textile, plastics, signage, woodworking | Pros: Versatile, good for non-metals; Cons: Lower speed for metal, sensitive optics |
High-Power Laser Cutting Machine | High wattage (above 6kW) for thick or hard materials | Heavy industry, shipbuilding, aerospace | Pros: Can cut thick/hard materials, boosts productivity; Cons: Higher cost, increased safety requirements |
Hybrid CNC Laser Cutting-Automation | Combines laser cutting with robotic automation | Large-scale metal fabrication, industrial parts | Pros: High productivity, labor saving; Cons: Requires skilled integration |
CNC Laser Engraving/Marking Machine | Focused on engraving and marking with high detail | Product identification, barcoding, branding | Pros: Precise, permanent marks; Cons: Mostly surface-level, slower throughput |
Fiber Laser CNC Cutting Machine
Fiber laser CNC cutting machines are designed for high-speed and precise metal cutting, making them ideal for industries such as automotive and electronics. Their solid-state design allows for lower operational costs and minimal maintenance, which is attractive for businesses focusing on efficiency. When sourcing these machines, buyers should assess power ratings, material compatibility, and the availability of local technical support, especially in regions with challenging logistics.
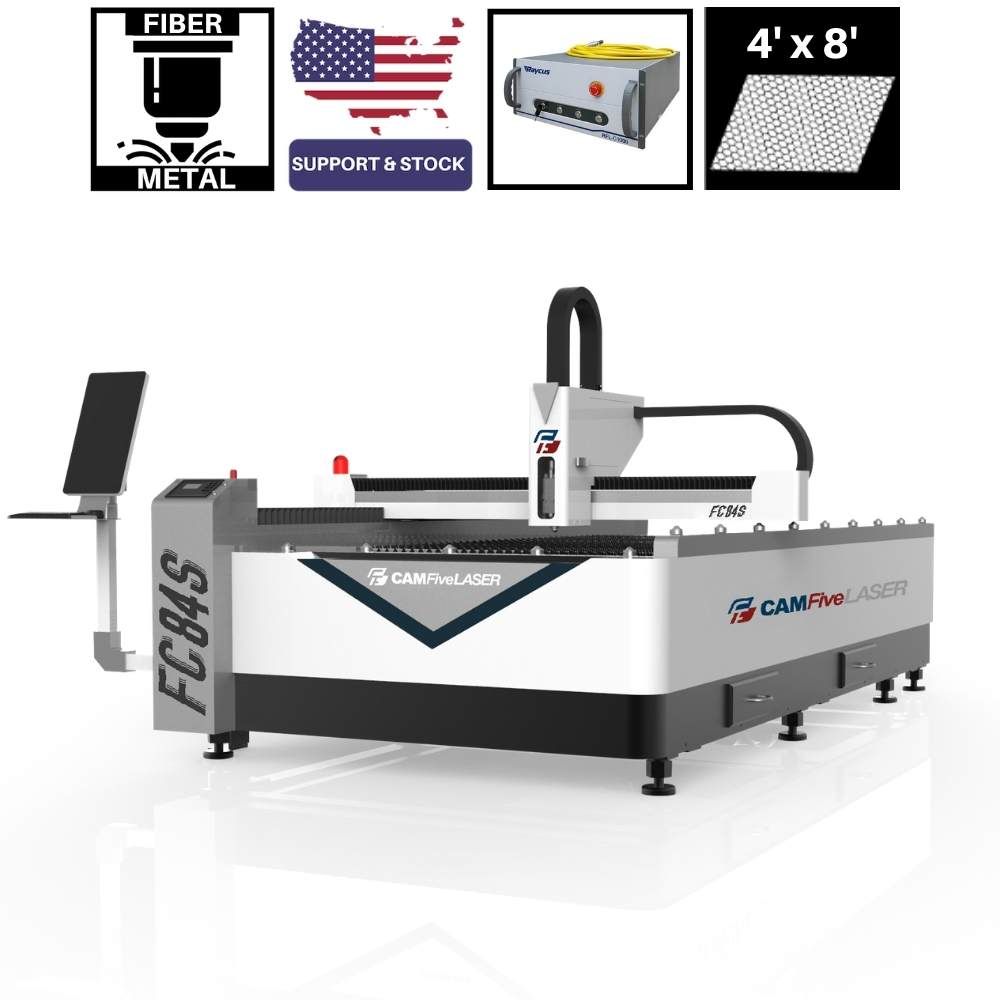
Illustrative Image (Source: Google Search)
CO₂ Laser CNC Cutting Machine
CO₂ laser CNC cutting machines utilize a gas-based laser, making them versatile for cutting various non-metal materials, including wood, plastics, and textiles. They excel in applications like signage and packaging but may operate slower on metals and require careful maintenance of optical components. B2B buyers should consider their specific material needs, ongoing maintenance requirements, and the availability of consumable gases when evaluating options.
High-Power Laser Cutting Machine
High-power laser cutting machines, typically rated above 6kW, are capable of cutting thick and hard materials, making them suitable for heavy industries such as shipbuilding and aerospace. Their ability to handle challenging materials boosts productivity but comes with a higher price tag and increased safety considerations. B2B buyers should evaluate the total cost of ownership, required safety measures, and the machine’s compatibility with their existing production processes.
Hybrid CNC Laser Cutting-Automation
Hybrid CNC laser cutting machines combine laser technology with robotic automation, significantly enhancing throughput for large-scale manufacturing. They are particularly beneficial for industrial parts fabrication where efficiency is paramount. However, these systems require skilled integration and may involve a steeper learning curve. Buyers should prioritize suppliers who offer comprehensive training and support to ensure smooth implementation.
CNC Laser Engraving/Marking Machine
CNC laser engraving and marking machines are designed for high-precision surface etching, ideal for product identification and branding. They provide permanent markings with minimal material removal, which is essential for traceability in regulated industries. Buyers should prioritize machines that offer robust software integration, high marking speeds, and compliance with global quality standards, particularly in sectors requiring strict adherence to regulations.
Related Video: Metal laser cutting machine LS7 | BLM GROUP
Key Industrial Applications of laser cnc machine for metal
Industry/Sector | Specific Application of laser cnc machine for metal | Value/Benefit for the Business | Key Sourcing Considerations for this Application |
---|---|---|---|
Automotive | Precision cutting of automotive components | Reduces material waste, enhances fit and assembly | Evaluate machine power, speed, and local support options |
Aerospace | Manufacturing of complex aircraft parts | Ensures high precision and compliance with safety standards | Consider certifications, maintenance needs, and part complexity |
Electronics | Custom metal fabrication for electronic enclosures | Facilitates rapid prototyping and reduces lead times | Assess material compatibility and software integration |
Heavy Machinery | Cutting thick steel for machinery frames | Increases productivity and reduces operational costs | Evaluate total cost of ownership and safety requirements |
Medical Devices | Production of surgical instruments and implants | Ensures precision and compliance with health regulations | Focus on machine accuracy and certifications for medical use |
Automotive
In the automotive industry, laser CNC machines are pivotal for precision cutting of components such as brackets, chassis parts, and intricate designs for bodywork. The high accuracy of laser cutting minimizes material waste and ensures that parts fit together seamlessly during assembly, which is crucial for vehicle performance and safety. B2B buyers should consider the machine’s power output and speed capabilities to meet production demands and ensure local technical support for maintenance.
Aerospace
Aerospace manufacturing requires adherence to stringent safety and quality standards, making laser CNC machines invaluable for producing complex components like wing structures and engine parts. These machines provide the precision necessary to maintain structural integrity while reducing lead times. Buyers in this sector should prioritize sourcing machines with relevant certifications and robust maintenance programs to ensure compliance with industry regulations.
Electronics
In the electronics sector, laser CNC machines facilitate the fabrication of custom metal enclosures and components that are essential for housing sensitive electronic devices. The ability to rapidly prototype designs allows companies to innovate quickly and respond to market demands. Buyers should evaluate the compatibility of machines with various materials and ensure that software integration supports their design processes for optimal efficiency.
Heavy Machinery
For the heavy machinery sector, laser CNC machines are employed to cut thick steel and other robust materials used in machinery frames and structural components. The efficiency of laser cutting leads to increased productivity and reduced operational costs, making it a preferred choice for manufacturers. Buyers should consider the total cost of ownership, including maintenance and safety requirements, to make informed purchasing decisions.
Medical Devices
In the medical field, laser CNC machines are used to produce surgical instruments and implants that require high precision and compliance with health regulations. The non-contact nature of laser cutting minimizes contamination risks, which is critical in medical applications. B2B buyers should focus on sourcing machines that offer exceptional accuracy and are certified for medical device manufacturing to ensure compliance with industry standards.
Related Video: How does the CNC Fiber laser cutting machine work? – Factories
Strategic Material Selection Guide for laser cnc machine for metal
When selecting materials for laser CNC machining in metalworking, it’s crucial for B2B buyers to understand the properties, advantages, and limitations of the most common materials. This knowledge allows for informed decisions that align with production requirements and market demands. Below, we analyze four prevalent materials used in laser CNC machining, focusing on their key properties, pros and cons, and considerations for international buyers.
Carbon Steel
Key Properties: Carbon steel is known for its high strength and durability, with a temperature rating that can withstand significant heat during machining. It typically exhibits good weldability and can be treated for enhanced corrosion resistance.
Pros & Cons: The primary advantage of carbon steel is its affordability and excellent mechanical properties, making it suitable for a wide range of applications, from automotive parts to structural components. However, it can be prone to rust if not properly coated or treated, which may necessitate additional processing steps.
Impact on Application: Carbon steel is compatible with various media, including oil and water-based coolants, which can enhance the cutting process. Its versatility makes it a common choice for industries requiring both strength and cost-effectiveness.
Considerations for International Buyers: Buyers should ensure compliance with local standards such as ASTM A36 or DIN 17100. In regions like Africa and South America, where environmental conditions may accelerate corrosion, additional protective coatings may be advisable.
Stainless Steel
Key Properties: Stainless steel is recognized for its excellent corrosion resistance and ability to withstand high temperatures. It typically contains chromium, which enhances its durability and aesthetic appeal.
Pros & Cons: The main advantage of stainless steel is its longevity and resistance to oxidation, making it ideal for applications in food processing, medical devices, and architectural components. However, it is generally more expensive than carbon steel and may require specialized cutting techniques due to its toughness.
Impact on Application: Stainless steel is compatible with a variety of media, including acidic and alkaline substances, which makes it suitable for industries that deal with corrosive environments. Its clean finish reduces the need for post-processing.
Considerations for International Buyers: Buyers in Europe and the Middle East should look for compliance with standards such as ASTM A240 or EN 10088. The higher cost may be justified by the material’s longevity and reduced maintenance needs.
Aluminum
Key Properties: Aluminum is lightweight yet strong, with excellent thermal and electrical conductivity. It is also resistant to corrosion, especially when anodized.
Pros & Cons: The key advantage of aluminum is its low weight, which is beneficial for applications in aerospace and automotive industries. However, it can be more expensive than steel and may require specific laser settings to avoid melting or warping during cutting.
Impact on Application: Aluminum’s compatibility with various media, including water and oil, allows for effective cooling during the cutting process. Its versatility makes it suitable for intricate designs and lightweight structures.
Considerations for International Buyers: Buyers should consider compliance with standards like ASTM B221 or JIS H4000. In regions like Nigeria, where aluminum is often used in construction, understanding local supply chains and availability is critical.
Brass
Key Properties: Brass is an alloy of copper and zinc, known for its excellent machinability and corrosion resistance. It has good thermal and electrical conductivity, making it suitable for various applications.
Pros & Cons: The primary advantage of brass is its aesthetic appeal and durability, making it ideal for decorative applications as well as plumbing and electrical fittings. However, its higher cost compared to steel and aluminum can be a limiting factor for some buyers.
Impact on Application: Brass is compatible with a range of media, including water and gas, which is essential for plumbing applications. Its low friction properties make it ideal for moving parts.
Considerations for International Buyers: Compliance with standards such as ASTM B36 or DIN 17660 is important. Buyers in Europe and the Middle East should also consider the availability of brass in local markets, as sourcing can vary significantly.
Material | Typical Use Case for laser cnc machine for metal | Key Advantage | Key Disadvantage/Limitation | Relative Cost (Low/Med/High) |
---|---|---|---|---|
Carbon Steel | Structural components, automotive parts | Cost-effective and strong | Prone to rust without treatment | Low |
Stainless Steel | Medical devices, food processing equipment | Excellent corrosion resistance | Higher cost and specialized cutting needed | High |
Aluminum | Aerospace, automotive lightweight structures | Lightweight and versatile | More expensive and specific laser settings | Medium |
Brass | Plumbing fittings, decorative applications | Aesthetic appeal and durability | Higher cost compared to steel and aluminum | High |
This strategic material selection guide provides a comprehensive overview for international B2B buyers, enabling them to make informed decisions that align with their operational needs and market conditions.
In-depth Look: Manufacturing Processes and Quality Assurance for laser cnc machine for metal
The manufacturing processes and quality assurance practices for laser CNC machines for metal are crucial for ensuring that buyers receive high-quality, reliable equipment. Understanding these processes allows B2B buyers to make informed decisions when sourcing laser cutting machines, particularly in diverse markets such as Africa, South America, the Middle East, and Europe.
Manufacturing Processes for Laser CNC Machines
1. Material Preparation
The manufacturing process begins with material preparation, which involves selecting high-grade materials that meet the specifications required for the laser CNC machine. Common materials include:
- Structural Steel: Often used for frames and supports due to its strength and durability.
- Aluminum Alloys: Lightweight and resistant to corrosion, suitable for various components.
- Optical Components: High-quality glass or crystal is essential for laser generation and focusing.
Material quality checks, such as dimensional inspections and metallurgical testing, are performed to ensure compliance with industry standards before proceeding to the next stage.
2. Forming
In this stage, the prepared materials are shaped into components through various techniques:
- Laser Cutting: Precise cutting of components using advanced laser technology, ensuring minimal waste and high accuracy.
- CNC Machining: Additional shaping of parts to achieve specific dimensions and tolerances.
- Bending and Forming: Some components may require bending to fit assembly requirements.
Each forming technique contributes to the overall precision and performance of the final machine. The choice of technique is often influenced by the machine’s intended applications and the specific material properties.
3. Assembly
The assembly stage involves integrating various components into a cohesive machine. This process includes:
- Mechanical Assembly: Connecting structural parts, such as frames, rails, and support systems.
- Electrical Assembly: Installing control systems, wiring, and power supplies.
- Optical Alignment: Ensuring that all optical components are properly aligned for effective laser performance.
Assembly is a critical phase where attention to detail is paramount. Misalignment or improper connections can lead to performance issues, affecting the machine’s overall efficiency and output.
4. Finishing
Finishing processes enhance the durability and aesthetics of the laser CNC machine. Key techniques include:
- Surface Treatment: Applying coatings or treatments to prevent corrosion and enhance appearance.
- Quality Inspections: Conducting visual and dimensional inspections to verify that all components meet specified tolerances and quality standards.
This stage ensures that the machine is not only functional but also meets the aesthetic and durability expectations of buyers.
Quality Assurance (QA) Standards
Quality assurance is vital in the manufacturing of laser CNC machines, as it ensures compliance with international and industry-specific standards. Key quality standards include:
- ISO 9001: This international standard sets the criteria for a quality management system (QMS) and is essential for ensuring consistent quality and customer satisfaction.
- CE Marking: Particularly important in Europe, CE marking indicates that the machine meets EU safety, health, and environmental protection requirements.
- API Standards: Relevant for machines used in the oil and gas sector, ensuring they meet industry-specific safety and performance criteria.
Quality Control Checkpoints
Effective quality control (QC) is implemented throughout the manufacturing process, typically at the following checkpoints:
- Incoming Quality Control (IQC): Inspections of raw materials upon arrival to verify compliance with specifications.
- In-Process Quality Control (IPQC): Regular checks during the manufacturing process to monitor quality and prevent defects.
- Final Quality Control (FQC): Comprehensive inspections and testing of the completed machine before shipment, ensuring it meets all operational specifications and standards.
Common Testing Methods
To validate the quality and performance of laser CNC machines, several testing methods are employed:
- Functional Testing: Assessing the machine’s operational capabilities, including speed, precision, and cutting quality.
- Safety Testing: Ensuring compliance with safety standards, including emergency stop functions and protective measures.
- Performance Testing: Evaluating the machine’s efficiency in various applications and materials.
Verifying Supplier Quality Control
B2B buyers should take proactive steps to verify the quality control measures of their suppliers. Key strategies include:
- Supplier Audits: Conducting on-site audits to assess the manufacturing processes, quality control practices, and overall operational efficiency.
- Requesting Quality Reports: Suppliers should provide documentation demonstrating compliance with international standards and internal QC protocols.
- Third-Party Inspections: Engaging independent inspection agencies to evaluate the machine’s quality and performance before finalizing purchases.
Quality Control and Certification Nuances for International Buyers
For international B2B buyers, understanding the nuances of quality control and certification is crucial. Factors to consider include:
- Regional Standards: Different regions may have varying standards and regulations. Buyers should ensure that the machines comply with local regulations in their respective countries (e.g., Nigeria, Italy).
- Documentation: Ensure that all necessary certifications and compliance documents are provided, as these may be required for customs clearance and regulatory compliance.
- Cultural Considerations: Recognizing and adapting to cultural differences in business practices can enhance communication and foster stronger supplier relationships.
By comprehensively understanding the manufacturing processes and quality assurance practices for laser CNC machines, B2B buyers can make informed decisions, reducing risks and ensuring they invest in reliable, high-quality machinery that meets their operational needs.
Comprehensive Cost and Pricing Analysis for laser cnc machine for metal Sourcing
When sourcing laser CNC machines for metal, understanding the comprehensive cost structure is essential for international B2B buyers. This analysis will highlight the key components of costs, the factors influencing pricing, and actionable tips for negotiating and optimizing purchases.
Cost Components
-
Materials: The primary cost driver in laser CNC machines is the quality of materials used in their construction. High-grade components such as precision optics, robust frames, and efficient laser sources can significantly increase the initial purchase price. Buyers should consider not just the upfront costs but also the long-term durability and performance of these materials.
-
Labor: Labor costs encompass both manufacturing and assembly. Skilled technicians are necessary for assembling high-precision machines. Additionally, ongoing labor costs for operation, maintenance, and potential training should be factored into the total cost of ownership.
-
Manufacturing Overhead: This includes indirect costs associated with production, such as utilities, facility maintenance, and administrative expenses. Buyers should inquire about the manufacturer’s efficiency in managing these costs, as they can influence final pricing.
-
Tooling: Custom tooling required for specific applications adds to the overall cost. Buyers should evaluate whether the machine’s design allows for easy adaptation to various tooling requirements, which can save money in the long run.
-
Quality Control (QC): Ensuring that machines meet specific standards involves additional QC processes. Machines with certifications (e.g., ISO, CE) may carry a premium but offer assurance of quality and reliability.
-
Logistics: Shipping costs can vary widely based on the machine’s size and weight, as well as the distance to the destination. International buyers should consider logistics partners and the potential for delays or additional tariffs.
-
Margin: Manufacturer margins will vary depending on their market positioning, brand reputation, and the level of customization offered. Understanding the typical margins in your specific market can help buyers negotiate more effectively.
Price Influencers
-
Volume/MOQ: Bulk purchasing often leads to significant discounts. Buyers should assess their needs and consider joining purchasing groups to leverage better pricing.
-
Specifications/Customization: Custom features can increase costs. Buyers should clearly define their requirements to avoid unnecessary expenses while ensuring the machine meets their operational needs.
-
Materials: The type of materials being cut can influence machine specifications and, consequently, pricing. For example, machines designed for heavy-duty materials may be more expensive.
-
Quality/Certifications: Machines with recognized certifications often command higher prices but provide assurance of quality. Buyers should weigh the benefits against their budget constraints.
-
Supplier Factors: The reputation and reliability of suppliers play a crucial role in pricing. Established suppliers with a proven track record may charge more but offer better support and service.
-
Incoterms: Understanding shipping terms is critical. Buyers should be clear on who bears responsibility for shipping costs, insurance, and risk during transport to avoid unexpected expenses.
Buyer Tips
-
Negotiation: Leverage your knowledge of market prices and competitor offerings when negotiating. Establishing long-term relationships with suppliers can also lead to better pricing and terms.
-
Cost-Efficiency: Consider the total cost of ownership (TCO), which includes maintenance, operational efficiency, and potential downtime costs. A higher upfront investment in a reliable machine may lead to lower TCO over time.
-
Pricing Nuances for International Buyers: Buyers from Africa, South America, the Middle East, and Europe should be aware of currency fluctuations and import tariffs that can affect final costs. It’s advisable to account for these factors in budgeting.
-
Disclaimer for Indicative Prices: Prices for laser CNC machines can vary significantly based on the factors mentioned above. It is crucial to obtain quotes from multiple suppliers and consider all aspects of the purchase to make informed decisions.
By understanding these components and influencers, B2B buyers can navigate the complexities of sourcing laser CNC machines for metal more effectively, ensuring they make sound investments that align with their operational needs and financial goals.
Essential Technical Properties and Trade Terminology for laser cnc machine for metal
Key Technical Properties of Laser CNC Machines for Metal
Understanding the critical specifications of laser CNC machines is essential for B2B buyers to make informed purchasing decisions. Here are some vital technical properties to consider:
-
Power Output (Watts)
– Definition: Measured in watts (W), the power output indicates the laser’s ability to cut through different metal thicknesses.
– B2B Importance: Higher wattage allows for faster cutting speeds and the ability to handle thicker materials. For industries like aerospace and automotive, where precision and speed are crucial, selecting the right power output can significantly impact production efficiency. -
Material Compatibility
– Definition: Refers to the types of metals that the CNC laser machine can effectively cut, such as carbon steel, stainless steel, aluminum, and brass.
– B2B Importance: Understanding material compatibility is essential for buyers to ensure the machine aligns with their production needs. Choosing a versatile machine that can handle various materials can reduce the need for multiple machines and save costs.
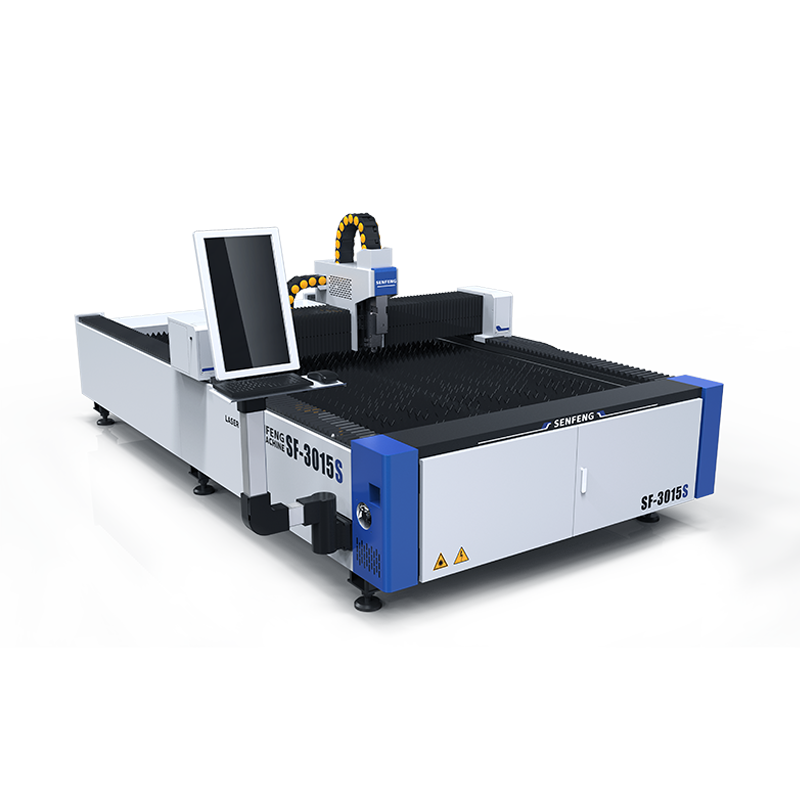
Illustrative Image (Source: Google Search)
-
Cutting Tolerance
– Definition: This specification indicates the precision of the cuts, typically measured in microns.
– B2B Importance: Tight tolerances are critical in industries requiring high precision, such as medical devices and aerospace components. A machine capable of maintaining low tolerances will enhance product quality and reduce waste. -
Table Size and Load Capacity
– Definition: The dimensions of the cutting table and the maximum weight it can support.
– B2B Importance: Adequate table size allows for larger workpieces, which is particularly important for industries that manufacture big components. Ensuring the load capacity matches production requirements prevents operational bottlenecks. -
Speed of Operation
– Definition: The rate at which the laser cutting machine can operate, usually measured in meters per minute (m/min).
– B2B Importance: Faster machines enhance productivity, allowing businesses to meet tight deadlines and large orders. Buyers should assess the speed in relation to their production volume to ensure it meets operational demands.
Common Trade Terminology in the Laser CNC Industry
Familiarity with industry jargon is crucial for effective communication and negotiation. Here are some common terms B2B buyers should know:
-
OEM (Original Equipment Manufacturer)
– Definition: A company that produces parts or equipment that may be marketed by another manufacturer.
– Relevance: Understanding OEM relationships is vital for buyers to ensure they are sourcing high-quality machines and components that meet industry standards. -
MOQ (Minimum Order Quantity)
– Definition: The smallest quantity of a product that a supplier is willing to sell.
– Relevance: Knowing the MOQ helps buyers plan their purchases effectively, especially when looking to stock inventory without incurring excessive costs. -
RFQ (Request for Quotation)
– Definition: A document sent to suppliers requesting a quote for specific products or services.
– Relevance: An RFQ is essential for B2B buyers to obtain competitive pricing and terms from multiple suppliers, enabling better negotiation outcomes. -
Incoterms (International Commercial Terms)
– Definition: A series of predefined commercial terms published by the International Chamber of Commerce (ICC) that clarify the responsibilities of buyers and sellers in international transactions.
– Relevance: Familiarity with Incoterms helps buyers understand shipping responsibilities, risks, and costs, ensuring smoother international transactions. -
Lead Time
– Definition: The time taken from placing an order to the delivery of the product.
– Relevance: Understanding lead times is critical for planning production schedules and managing supply chain efficiencies, particularly in industries where timing is crucial.
By grasping these technical properties and trade terms, international B2B buyers can enhance their procurement strategies, streamline operations, and foster successful partnerships in the laser CNC machine market.
Navigating Market Dynamics, Sourcing Trends, and Sustainability in the laser cnc machine for metal Sector
Market Overview & Key Trends
The laser CNC machine market for metal is experiencing robust growth driven by several global factors. Key drivers include the increasing demand for precision manufacturing across industries such as automotive, aerospace, and electronics, where the ability to produce intricate designs quickly and efficiently is paramount. The rise of Industry 4.0 is also influencing market dynamics, as manufacturers seek to integrate smart technologies and automation into their production processes. This trend is particularly relevant for international B2B buyers from regions like Africa, South America, the Middle East, and Europe, where competition is intensifying, and operational efficiency is critical for maintaining a competitive edge.
Emerging technologies such as fiber lasers, which offer higher efficiency and lower operational costs, are gaining traction. Additionally, the shift towards higher power outputs is enabling manufacturers to process thicker materials more effectively, catering to industries that require heavy-duty applications. Buyers should also be aware of the trend toward automated material handling systems, which enhance productivity by reducing downtime and labor costs. As businesses increasingly prioritize sustainability, there is a growing focus on energy-efficient solutions that minimize waste and environmental impact, influencing purchasing decisions.
For B2B buyers, understanding these market dynamics is essential for making informed sourcing decisions. By aligning procurement strategies with these trends, companies can not only enhance their production capabilities but also position themselves as leaders in their respective markets.
Sustainability & Ethical Sourcing in B2B
Sustainability is becoming a cornerstone of procurement strategies in the laser CNC machine sector. The environmental impact of manufacturing processes, including energy consumption and waste generation, is under scrutiny. International B2B buyers must consider machines that incorporate energy-efficient technologies and sustainable practices. This includes selecting suppliers who utilize renewable energy sources and have robust waste management systems in place.
Ethical sourcing is equally important, as buyers are increasingly held accountable for the social and environmental practices of their suppliers. Companies should prioritize partnerships with manufacturers that demonstrate transparency in their supply chains and adhere to ethical labor practices. Certifications such as ISO 14001 (Environmental Management) and ISO 45001 (Occupational Health and Safety) can serve as indicators of a supplier’s commitment to sustainability and ethical standards.
Furthermore, buyers should look for “green” certifications for the materials used in laser CNC machines, such as recycled metals or eco-friendly coatings. By prioritizing sustainability and ethical sourcing, B2B buyers not only reduce their environmental footprint but also enhance their brand reputation, appealing to an increasingly conscientious consumer base.
Brief Evolution/History
The evolution of laser CNC machines for metal cutting dates back to the 1960s when the first lasers were developed for industrial applications. Initially, CO₂ lasers dominated the market due to their versatility and ability to cut non-metal materials. However, the introduction of fiber lasers in the late 2000s marked a significant shift, providing higher efficiency and lower maintenance costs, particularly for metal applications. This technological advancement has allowed manufacturers to achieve greater precision and speed in their production processes.
Over the years, the integration of CNC technology has further transformed the landscape, enabling automated control of laser cutting processes. As industries continue to evolve and embrace Industry 4.0 principles, the future of laser CNC machines looks promising, with ongoing innovations in power outputs, automation, and sustainability practices shaping the next generation of manufacturing solutions. B2B buyers should stay abreast of these developments to leverage the best technologies for their operational needs.
Frequently Asked Questions (FAQs) for B2B Buyers of laser cnc machine for metal
-
What factors should I consider when vetting suppliers for laser CNC machines?
When vetting suppliers, prioritize their experience, reputation, and customer reviews. Look for manufacturers with a proven track record in the laser CNC machine industry, particularly those that cater to your specific metalworking needs. Assess their certifications (ISO, CE) to ensure compliance with international quality standards. Additionally, inquire about their technical support capabilities, availability of spare parts, and after-sales service. Establishing a good rapport with suppliers can facilitate smoother communication and support throughout the purchasing process. -
Can laser CNC machines be customized to fit my specific production requirements?
Yes, many manufacturers offer customization options for laser CNC machines to meet specific production needs. Customizations can include modifications in power output, cutting size, and additional features like automation or software integration. It’s essential to communicate your requirements clearly during the initial discussions. Request detailed technical specifications and feasibility studies from the supplier to ensure that the customized machine aligns with your operational goals and production capabilities. -
What are the typical minimum order quantities (MOQ) and lead times for laser CNC machines?
Minimum order quantities for laser CNC machines can vary significantly based on the manufacturer and the complexity of the machine. Generally, MOQs range from one machine for smaller suppliers to bulk orders for larger manufacturers. Lead times can also vary, typically ranging from a few weeks to several months, depending on the machine’s specifications and the supplier’s production capacity. Always confirm these details upfront and consider any potential delays in shipping and customs clearance, particularly for international orders. -
What payment terms should I expect when sourcing laser CNC machines internationally?
Payment terms for international purchases can differ among suppliers. Common arrangements include upfront deposits (20-50% of the total price), with the balance due before shipment or upon delivery. Be cautious of suppliers that demand full payment in advance. Additionally, consider using secure payment methods such as letters of credit or escrow services to protect your investment. Clarify all payment details, including currency, payment methods, and any potential additional fees, before finalizing the contract. -
How do I ensure quality assurance and certifications for the laser CNC machines I purchase?
To ensure quality assurance, request documentation of the machine’s certifications, such as ISO 9001 or CE marking, which indicate compliance with international quality and safety standards. Additionally, ask for test results or quality control reports from previous production batches. It’s advisable to perform factory audits or inspections before shipment to verify the quality of the machines. Establishing clear quality expectations in your contract can help mitigate risks associated with subpar products. -
What logistical considerations should I keep in mind when importing laser CNC machines?
When importing laser CNC machines, consider logistics aspects such as shipping methods, customs duties, and import regulations in your country. Choose a reliable freight forwarder experienced in handling heavy machinery to ensure safe and timely delivery. Be aware of potential delays in customs clearance and factor in local regulations that may require additional documentation or inspections. It’s also wise to have a contingency plan in case of unexpected shipping challenges. -
How can I handle disputes or issues with suppliers during the procurement process?
To handle disputes effectively, maintain open communication with your supplier throughout the procurement process. Document all agreements, specifications, and correspondence to create a clear record of expectations. In the event of a dispute, attempt to resolve the issue amicably through negotiation first. If resolution is not possible, refer to the contract’s dispute resolution clause, which may include arbitration or mediation processes. Establishing a strong relationship with the supplier can also help prevent conflicts from escalating. -
What are the best practices for maintenance and support after purchasing a laser CNC machine?
After purchasing a laser CNC machine, establish a regular maintenance schedule to ensure optimal performance and longevity. Request a comprehensive maintenance manual from the supplier that includes guidelines for routine checks, cleaning, and parts replacement. It’s also beneficial to train your staff on proper operation and maintenance procedures to minimize risks and improve efficiency. Ensure that you have access to technical support from the supplier for troubleshooting and repairs, and consider investing in a service contract for ongoing support.
Important Disclaimer & Terms of Use
⚠️ Important Disclaimer
The information provided in this guide, including content regarding manufacturers, technical specifications, and market analysis, is for informational and educational purposes only. It does not constitute professional procurement advice, financial advice, or legal advice.
While we have made every effort to ensure the accuracy and timeliness of the information, we are not responsible for any errors, omissions, or outdated information. Market conditions, company details, and technical standards are subject to change.
B2B buyers must conduct their own independent and thorough due diligence before making any purchasing decisions. This includes contacting suppliers directly, verifying certifications, requesting samples, and seeking professional consultation. The risk of relying on any information in this guide is borne solely by the reader.
Strategic Sourcing Conclusion and Outlook for laser cnc machine for metal
In today’s competitive manufacturing landscape, the strategic sourcing of laser CNC machines for metal is essential for international B2B buyers. By understanding the diverse types of machines available—such as fiber and CO₂ lasers—buyers can make informed decisions tailored to their specific operational needs. The key takeaways include evaluating power outputs, ensuring material compatibility, and considering total cost of ownership.
Investing in the right laser CNC technology not only enhances precision and efficiency but also reduces waste and streamlines production processes. As industries across Africa, South America, the Middle East, and Europe strive for innovation, establishing partnerships with reputable suppliers is paramount.
Looking ahead, the demand for advanced laser cutting technology will continue to grow, driven by trends in automation and smart manufacturing. B2B buyers are encouraged to embrace this evolution, leveraging the insights from this guide to position their businesses for sustainable growth. Now is the time to explore the transformative potential of laser CNC machines, ensuring your operations remain at the forefront of the global market.