Your Ultimate Guide to Sourcing Six Axis Cnc Machine
Introduction: Navigating the Global Market for six axis cnc machine
In an increasingly competitive landscape, the six-axis CNC machine stands out as a game-changer for manufacturers seeking precision, versatility, and efficiency. This advanced technology enables the creation of complex geometries and intricate designs that traditional machines cannot achieve, making it indispensable for industries such as aerospace, automotive, and medical manufacturing. As B2B buyers from regions like Africa, South America, the Middle East, and Europe evaluate their sourcing options, understanding the nuances of six-axis CNC machines becomes critical for informed decision-making.
This comprehensive guide delves into the multifaceted world of six-axis CNC machines, covering essential aspects such as types of machines, materials compatible with CNC machining, manufacturing and quality control processes, reputable suppliers, cost considerations, and market trends. Each section is designed to provide actionable insights that empower international buyers to navigate the global market effectively.
By equipping yourself with in-depth knowledge and best practices outlined in this guide, you can streamline your procurement processes, mitigate risks associated with sourcing, and enhance your operational capabilities. Whether you are looking to enhance production efficiency or expand your manufacturing capabilities, this resource will serve as your roadmap to successfully leveraging six-axis CNC technology in your business.
Understanding six axis cnc machine Types and Variations
Type Name | Key Distinguishing Features | Primary B2B Applications | Brief Pros & Cons for Buyers |
---|---|---|---|
Articulated Arm CNC | Flexible joints, mimics human arm movement | Automotive, aerospace, and robotics | Pros: High versatility; Cons: Complex programming required. |
Delta CNC | Lightweight, high-speed, parallel kinematics | Packaging, food processing, electronics | Pros: Fast operation; Cons: Limited payload capacity. |
Scara CNC | Horizontal arm with vertical movement capability | Assembly lines, electronics, and medical | Pros: Efficient for pick-and-place; Cons: Less suitable for heavy materials. |
Gantry CNC | Large frame with dual axes for heavy workloads | Construction, metalworking, and woodworking | Pros: Handles large parts; Cons: Requires significant floor space. |
Hybrid CNC | Combines additive and subtractive manufacturing | Aerospace, automotive, and prototyping | Pros: Versatile production; Cons: Higher initial investment. |
Articulated Arm CNC
Articulated arm CNC machines are designed to replicate human arm movements, featuring multiple joints for enhanced flexibility. These machines excel in applications requiring intricate movements, such as in automotive and aerospace manufacturing, where precision is paramount. B2B buyers should consider the complexity of programming and the need for skilled operators, which can increase operational costs. However, their versatility makes them invaluable in environments where adaptability is crucial.
Delta CNC
Delta CNC machines are characterized by their lightweight structure and parallel kinematics, allowing for rapid movement and high-speed operations. Commonly used in packaging and food processing industries, these machines can handle repetitive tasks efficiently. Buyers should note the limited payload capacity, which may restrict their use in heavier applications. Nonetheless, the speed and precision of Delta CNC machines often lead to increased productivity and reduced cycle times.
Scara CNC
The SCARA (Selective Compliance Assembly Robot Arm) CNC machine features a unique design that allows for horizontal movement with vertical capabilities. This makes it particularly effective for assembly lines and applications in electronics and medical device manufacturing. While SCARA machines excel in speed and efficiency for pick-and-place tasks, they are less suited for handling heavier materials. B2B buyers should weigh the benefits of increased throughput against the limitations in material handling.
Gantry CNC
Gantry CNC machines utilize a large frame to support dual axes, making them ideal for processing large and heavy materials. They are widely used in construction, metalworking, and woodworking applications, where precision and strength are essential. Buyers should consider the significant floor space required for installation and operation. However, the ability to manage large parts efficiently often justifies the investment, particularly for businesses focusing on large-scale production.
Hybrid CNC
Hybrid CNC machines integrate both additive and subtractive manufacturing processes, offering unparalleled versatility for various applications, including aerospace, automotive, and prototyping. This type allows manufacturers to produce complex geometries and reduce material waste. However, the initial investment can be higher due to the sophisticated technology involved. B2B buyers should evaluate their production needs and potential return on investment, as the flexibility of hybrid machines can lead to significant long-term savings and innovation in product development.
Related Video: BACCI – 6 AXES CNC MACHINING CENTRE MODEL ARTIST.JET
Key Industrial Applications of six axis cnc machine
Industry/Sector | Specific Application of six axis cnc machine | Value/Benefit for the Business | Key Sourcing Considerations for this Application |
---|---|---|---|
Aerospace | Precision component manufacturing | High accuracy and reduced material waste | Certification requirements, supplier reputation |
Automotive | Complex part fabrication | Faster production cycles and enhanced design flexibility | Compliance with industry standards, after-sales support |
Medical Devices | Custom prosthetics and implants | Tailored solutions for patient-specific needs | Material biocompatibility, regulatory certifications |
Electronics | Circuit board and housing production | High precision and efficient mass production | Supplier technology capabilities, lead time reliability |
Energy | Turbine blade manufacturing | Improved efficiency and performance of energy systems | Material sourcing, sustainability practices |
Aerospace
In the aerospace sector, six-axis CNC machines are vital for manufacturing precision components like engine parts and structural elements. These machines enable intricate designs while maintaining tight tolerances, thereby reducing material waste. International buyers should consider the machine’s certification, as aerospace components must meet strict regulatory standards. Additionally, evaluating the supplier’s reputation in delivering quality and timely products is crucial to ensure compliance with industry requirements.
Automotive
The automotive industry benefits significantly from six-axis CNC machines for fabricating complex parts, such as engine blocks and transmission housings. These machines facilitate faster production cycles and allow for more intricate designs than traditional methods. For international buyers, understanding the compliance with automotive industry standards, such as ISO/TS 16949, is essential. Furthermore, after-sales support and the ability to adapt to new designs quickly can be key factors in supplier selection.
Medical Devices
In medical device manufacturing, six-axis CNC machines are used to create custom prosthetics and implants tailored to individual patient needs. This application requires high precision and the ability to work with biocompatible materials. Buyers must ensure that suppliers can provide the necessary regulatory certifications, such as ISO 13485, which pertains to quality management systems in the medical device sector. Additionally, understanding the supplier’s capabilities in material sourcing and customization is vital for meeting specific medical requirements.
Electronics
The electronics sector utilizes six-axis CNC machines for producing circuit boards and enclosures, where precision is paramount. These machines enhance efficiency in mass production while ensuring that intricate designs are executed flawlessly. International buyers should assess the technological capabilities of potential suppliers to ensure they can meet the required precision and volume. Moreover, lead time reliability is crucial to maintaining production schedules, especially in fast-paced electronics markets.
Energy
In the energy sector, six-axis CNC machines play a critical role in manufacturing turbine blades, which require precise engineering to optimize performance. These machines help improve the efficiency and reliability of energy systems. Buyers should consider the sourcing of materials, as the performance of turbine blades is closely linked to the quality of the materials used. Additionally, sustainability practices of suppliers are increasingly important, especially in regions prioritizing green energy solutions.
Related Video: CNC Machining – 3, 4 & 5th Axis? Explained
Strategic Material Selection Guide for six axis cnc machine
When selecting materials for six-axis CNC machines, it’s essential to consider various factors that impact performance, durability, and cost-efficiency. Below, we analyze four common materials used in the construction and components of six-axis CNC machines, focusing on their properties, advantages, disadvantages, and specific considerations for international B2B buyers.
Aluminum Alloys
Key Properties: Aluminum alloys are lightweight yet strong, offering excellent corrosion resistance and good thermal conductivity. They typically have a temperature rating up to 150°C and can withstand moderate pressure.
Pros & Cons: The primary advantages of aluminum alloys include their low weight, which enhances machine agility, and their resistance to rust, making them suitable for various environments. However, they can be more expensive than some alternatives and may not withstand high-stress applications as effectively as steel.
Impact on Application: Aluminum is particularly suitable for components that require high precision and low weight, such as frames and brackets. It is compatible with various machining processes, including milling and drilling.
Considerations for International Buyers: Buyers in regions like Africa and the Middle East should ensure compliance with local standards, which may include ASTM or JIS specifications. Additionally, sourcing aluminum from local suppliers can mitigate shipping costs and delays.
Steel Alloys
Key Properties: Steel alloys are known for their high strength and durability, with temperature ratings often exceeding 300°C. They exhibit excellent wear resistance and can handle high-pressure applications.
Pros & Cons: The key advantage of steel alloys is their robustness, making them ideal for heavy-duty applications. However, they are heavier than aluminum, which can affect the machine’s speed and agility. The cost can also be higher, particularly for high-grade alloys.
Impact on Application: Steel is often used in the structural components of CNC machines, such as the base and support frames, where strength is crucial. It is compatible with a wide range of machining processes.
Considerations for International Buyers: Buyers from Europe and South America should consider the availability of specific steel grades that meet local compliance standards, such as DIN or ASTM. The procurement of high-quality steel can also influence the overall cost and performance of the machine.
Composite Materials
Key Properties: Composites, such as carbon fiber or fiberglass, offer a unique combination of low weight and high strength. They are resistant to corrosion and have temperature ratings that can vary widely based on the resin used.
Pros & Cons: The primary advantage of composites is their lightweight nature, which can significantly improve machine dynamics. However, they often come at a higher cost and can require more complex manufacturing processes, which may increase lead times.
Impact on Application: Composites are particularly useful in applications requiring high stiffness and low weight, such as in aerospace components produced by CNC machines. Their compatibility with various machining techniques makes them versatile.
Considerations for International Buyers: Buyers in regions like Turkey and Egypt should be aware of the specific regulations regarding composite materials, which may differ from traditional metals. Ensuring compliance with international standards can facilitate smoother operations.
Plastics
Key Properties: Engineering plastics, such as nylon or polycarbonate, are lightweight and offer good chemical resistance. They can typically withstand temperatures up to 100°C, depending on the type.
Pros & Cons: Plastics are cost-effective and can be easily machined, making them suitable for prototyping and low-volume production. However, they may not provide the same level of strength or durability as metals, limiting their use in high-stress applications.
Impact on Application: Plastics are often used for non-structural components, such as housings and covers, where weight savings are important. They can also be used in applications requiring good insulation properties.
Considerations for International Buyers: Buyers from South America should consider the availability of specific plastic grades that meet local compliance standards. Additionally, understanding the recycling and disposal regulations for plastics in their region can enhance sustainability efforts.
Summary Table
Material | Typical Use Case for six axis cnc machine | Key Advantage | Key Disadvantage/Limitation | Relative Cost (Low/Med/High) |
---|---|---|---|---|
Aluminum Alloys | Frames and brackets | Lightweight and corrosion-resistant | Higher cost and lower stress capacity | Medium |
Steel Alloys | Structural components | High strength and durability | Heavier and potentially more expensive | High |
Composite Materials | Aerospace components | Low weight and high stiffness | Higher cost and complex manufacturing | High |
Plastics | Non-structural components | Cost-effective and easy to machine | Limited strength and durability | Low |
This strategic material selection guide provides essential insights for international B2B buyers, enabling informed decisions that align with their operational needs and compliance requirements.
In-depth Look: Manufacturing Processes and Quality Assurance for six axis cnc machine
Manufacturing Processes for Six Axis CNC Machines
The manufacturing of six axis CNC machines involves several critical stages, each contributing to the overall functionality and precision of the final product. Understanding these processes can help B2B buyers make informed decisions when evaluating suppliers.
1. Material Preparation
The first step in manufacturing six axis CNC machines is material preparation. High-quality materials such as stainless steel, aluminum, and specialized alloys are commonly used due to their durability and resistance to wear.
- Material Selection: It is essential to choose materials that not only meet the mechanical requirements but also comply with international standards relevant to the buyer’s region.
- Cutting and Shaping: Techniques such as laser cutting, water jet cutting, and plasma cutting are employed to create the initial components. Precision in this stage is crucial to minimize waste and ensure that parts fit together seamlessly.
2. Forming
Once the materials are prepared, they undergo various forming processes.
- Machining: This includes operations like milling, turning, and grinding, which shape the components to their required specifications. Advanced CNC machines are utilized to ensure high accuracy and repeatability.
- Welding and Assembly: For components that require joining, welding techniques such as TIG or MIG welding are employed. The assembly stage follows, where individual parts are carefully put together to form the machine structure.
3. Assembly
The assembly process is where the machine begins to take its final form.
- Sub-Assembly: Key components such as the spindle, tool holders, and control systems are assembled separately before being integrated into the main body of the CNC machine.
- Integration: This stage involves the installation of electrical and software components, ensuring that the machine’s operational capabilities align with industry requirements.
4. Finishing
The finishing stage enhances both the aesthetics and functionality of the CNC machine.
- Surface Treatment: Processes such as anodizing, powder coating, or painting are applied to protect against corrosion and enhance durability.
- Calibration and Testing: Each machine is calibrated to ensure it meets the specified tolerances. This includes setting up the control systems and running initial test cycles.
Quality Assurance in Manufacturing
Quality assurance is a vital aspect of the manufacturing process for six axis CNC machines. Establishing robust quality control (QC) measures helps ensure that machines meet both international standards and customer expectations.
International Standards
B2B buyers should be aware of the following international standards that govern the quality of CNC machines:
- ISO 9001: This standard focuses on quality management systems and is a prerequisite for many buyers. Suppliers certified under ISO 9001 demonstrate a commitment to continuous improvement and customer satisfaction.
- CE Marking: Particularly relevant for European buyers, CE marking indicates compliance with health, safety, and environmental protection standards.
- API Standards: For industries such as oil and gas, API certification ensures that the equipment meets stringent operational requirements.
QC Checkpoints
Quality control involves several critical checkpoints throughout the manufacturing process:
- Incoming Quality Control (IQC): This initial checkpoint ensures that materials and components received from suppliers meet specified quality standards before processing begins.
- In-Process Quality Control (IPQC): During manufacturing, regular inspections are conducted to monitor the production process and identify any deviations from set standards.
- Final Quality Control (FQC): After assembly, a comprehensive inspection is performed to validate that the machine operates correctly and meets all specifications.
Common Testing Methods
Testing methods used during the quality assurance process include:
- Functional Testing: Verifying that the CNC machine operates as intended, including checking movement along all six axes.
- Dimensional Inspection: Using tools like calipers and laser measuring systems to ensure parts adhere to design specifications.
- Performance Testing: Assessing the machine’s capabilities in real-world scenarios to ensure it meets operational requirements.
Verifying Supplier Quality Control
B2B buyers must take proactive steps to verify the quality control practices of potential suppliers. Here are some actionable insights:
- Conduct Audits: Regular audits of supplier facilities can provide insight into their manufacturing processes and adherence to quality standards. This can be done through on-site visits or third-party services.
- Request Quality Reports: Suppliers should be able to provide documentation of their quality control processes, including results from IQC, IPQC, and FQC stages. This transparency is crucial for building trust.
- Engage Third-Party Inspectors: Utilizing independent inspection services can help validate the quality of the machines before they are shipped. This is particularly important for buyers in regions where local expertise may be limited.
QC/Cert Nuances for International B2B Buyers
When engaging with suppliers from different regions, B2B buyers should be aware of specific nuances related to quality control and certifications:
- Cultural Differences: Different countries may have varying approaches to quality assurance. Understanding these cultural factors can aid in better communication and expectation management.
- Regulatory Compliance: Buyers should ensure that suppliers are compliant with local regulations in their respective regions, which may differ from international standards.
- Language Barriers: Clear communication is vital; therefore, buyers may consider working with suppliers who can provide documentation and support in their preferred language.
By comprehensively understanding the manufacturing processes and quality assurance practices associated with six axis CNC machines, B2B buyers can make more informed decisions when selecting suppliers, ensuring they receive high-quality equipment that meets their operational needs.
Related Video: SMART Quality Control for Manufacturing
Comprehensive Cost and Pricing Analysis for six axis cnc machine Sourcing
When sourcing a six axis CNC machine, understanding the comprehensive cost structure and pricing analysis is crucial for international B2B buyers. This analysis will help you navigate the complexities of sourcing and ensure you make informed purchasing decisions.
Cost Components
-
Materials: The cost of raw materials is a significant factor in the overall pricing of CNC machines. High-quality steel, aluminum, and electronics directly affect durability and performance. Ensure that the materials meet industry standards to avoid future repair costs.
-
Labor: Labor costs vary widely depending on the country of manufacture. Regions with higher labor costs may produce machines with better craftsmanship and quality assurance. Conversely, sourcing from countries with lower labor costs can reduce upfront expenses, but may lead to increased maintenance costs if quality is compromised.
-
Manufacturing Overhead: This includes all indirect costs associated with production, such as utilities, rent, and administrative expenses. These costs can vary significantly by region, impacting the final price of the machine.
-
Tooling: Specialized tooling required for CNC machining adds to the initial cost. The complexity of the machine design will determine the tooling costs. Buyers should consider whether the supplier can provide tooling as part of the package or if it will need to be sourced separately.
-
Quality Control (QC): Implementing stringent QC processes can increase costs but is essential for ensuring the machine meets performance specifications. Look for suppliers that have ISO certifications or similar quality standards, as this can provide assurance of the machine’s reliability.
-
Logistics: Transportation and shipping costs are critical, especially for international buyers. Factors such as distance, shipping method, and customs duties can significantly impact the total cost. Incoterms will also play a role in determining who bears these costs.
-
Margin: Suppliers will typically add a margin to cover their costs and generate profit. Understanding the market average for margins in CNC machine sales can help buyers identify reasonable pricing.
Price Influencers
-
Volume/MOQ: Ordering in bulk can lead to significant cost reductions per unit. Suppliers often have minimum order quantities (MOQs) that can affect pricing structures.
-
Specifications/Customization: Custom machines or those with advanced specifications will generally cost more. Buyers should carefully assess whether customization is necessary for their operations.
-
Materials: The choice of materials can greatly influence the price. For instance, using high-grade materials will increase costs but may enhance longevity and performance.
-
Quality/Certifications: Machines with recognized quality certifications may command higher prices, but they often offer better reliability and support.
-
Supplier Factors: The reputation and reliability of the supplier can influence pricing. Established suppliers may charge more, but they often provide better support and warranty options.
-
Incoterms: The chosen Incoterms can affect the total cost by determining who is responsible for shipping, insurance, and customs duties. Familiarize yourself with terms like FOB (Free On Board) and CIF (Cost, Insurance, and Freight) to make informed decisions.
Buyer Tips
-
Negotiation: Always negotiate prices and terms with suppliers. Be prepared to discuss volume discounts, payment terms, and delivery schedules.
-
Cost-Efficiency: Consider the Total Cost of Ownership (TCO), which includes purchase price, maintenance, and operational costs. A cheaper machine may not be cost-effective in the long run if it requires frequent repairs or has higher operational costs.
-
Pricing Nuances: Be aware of regional pricing differences, especially when sourcing from Africa, South America, the Middle East, and Europe. Currency fluctuations and local economic conditions can impact pricing.
-
Supplier Research: Conduct thorough research on potential suppliers. Look for reviews, case studies, and customer testimonials to gauge their reliability and quality.
Disclaimer
Prices in this analysis are indicative and can vary based on market conditions, supplier negotiations, and specific buyer requirements. Always conduct thorough due diligence before finalizing a purchase.
Essential Technical Properties and Trade Terminology for six axis cnc machine
When considering the acquisition of a six-axis CNC machine, understanding its technical properties and the relevant trade terminology is crucial for making informed decisions. Below are essential specifications and terms that B2B buyers, particularly from regions like Africa, South America, the Middle East, and Europe, should be familiar with.
Key Technical Properties
-
Material Grade
– Definition: The classification of materials used in the machine’s construction, such as stainless steel or aluminum alloys.
– Importance: The material grade impacts the machine’s durability, weight, and resistance to wear and corrosion. Selecting the right material ensures longevity and performance, reducing maintenance costs and downtime. -
Tolerance
– Definition: The allowable deviation from a standard dimension in the machined part.
– Importance: High tolerance levels are critical in precision manufacturing. For international buyers, understanding tolerance requirements helps ensure that the products meet industry standards and customer expectations, which is vital for competitive advantage. -
Axis Configuration
– Definition: Refers to the arrangement and movement capabilities of the machine’s axes; in a six-axis machine, there are three linear axes (X, Y, Z) and three rotational axes (A, B, C).
– Importance: The axis configuration determines the machine’s versatility and complexity in machining operations. A six-axis configuration allows for intricate designs and complex geometries, making it suitable for diverse applications across various industries. -
Spindle Speed
– Definition: The rotational speed of the spindle, usually measured in revolutions per minute (RPM).
– Importance: Higher spindle speeds can improve machining efficiency and surface finish quality. B2B buyers should consider spindle speed when evaluating the machine’s capabilities for specific materials and production needs. -
Feed Rate
– Definition: The speed at which the machine tool moves through the material, typically measured in units per minute (e.g., mm/min).
– Importance: Understanding the feed rate is essential for optimizing production speed and quality. A higher feed rate can lead to increased productivity, but it must be balanced with the desired precision.
Common Trade Terminology
-
OEM (Original Equipment Manufacturer)
– Definition: A company that produces parts or equipment that may be marketed by another manufacturer.
– Relevance: Understanding OEM relationships can help buyers identify reliable suppliers who provide high-quality components, essential for maintaining the machine’s performance and warranty. -
MOQ (Minimum Order Quantity)
– Definition: The smallest quantity of a product that a supplier is willing to sell.
– Relevance: Knowing the MOQ helps buyers plan their purchasing strategy, especially in bulk buying scenarios, which can lead to cost savings and better negotiation leverage. -
RFQ (Request for Quotation)
– Definition: A document issued by a buyer to request pricing and other details from suppliers.
– Relevance: An effective RFQ process is crucial for obtaining competitive pricing and terms. It allows buyers to compare offers and make informed purchasing decisions. -
Incoterms
– Definition: International commercial terms that define the responsibilities of buyers and sellers in international transactions.
– Relevance: Familiarity with Incoterms is vital for international buyers to understand shipping responsibilities, risks, and costs, ensuring smooth logistics and compliance with trade regulations. -
Lead Time
– Definition: The amount of time it takes from placing an order to receiving the product.
– Relevance: Understanding lead times is essential for planning production schedules and inventory management. It helps buyers avoid delays that could impact their operations.
Conclusion
By grasping these essential technical properties and trade terminology related to six-axis CNC machines, B2B buyers can enhance their procurement strategies, ensure quality, and foster strong supplier relationships. This knowledge is instrumental in navigating the complexities of international trade and optimizing manufacturing processes.
Navigating Market Dynamics, Sourcing Trends, and Sustainability in the six axis cnc machine Sector
Market Overview & Key Trends
The global market for six-axis CNC machines is witnessing significant transformation driven by technological advancements and shifting consumer demands. Key drivers include the increasing need for precision manufacturing across various sectors such as aerospace, automotive, and medical devices. The rise of Industry 4.0 has led to greater integration of automation and data exchange, prompting manufacturers to adopt more sophisticated CNC technologies. International B2B buyers from Africa, South America, the Middle East, and Europe should note the growing trend towards smart manufacturing, which emphasizes the use of IoT-enabled machines that enhance productivity and reduce downtime.
Emerging sourcing trends highlight a move towards local and regional suppliers, particularly in response to global supply chain disruptions. Buyers are increasingly prioritizing suppliers who can offer not just competitive pricing but also reliable delivery timelines. In regions like Turkey and Egypt, there is a burgeoning market for domestic CNC machine manufacturers, presenting an opportunity for B2B buyers to engage with local suppliers who understand regional challenges and can provide tailored solutions.
Moreover, sustainability is becoming a critical factor in purchasing decisions. Buyers are now looking for CNC machines that minimize waste and energy consumption. The integration of eco-friendly practices in manufacturing processes is not just a regulatory requirement but a competitive differentiator in the global market. Understanding these dynamics is essential for international buyers to navigate the complexities of sourcing six-axis CNC machines effectively.
Sustainability & Ethical Sourcing in B2B
As the spotlight on environmental sustainability intensifies, B2B buyers in the six-axis CNC machine sector must consider the environmental impact of their sourcing decisions. The manufacturing of CNC machines often involves energy-intensive processes and the use of non-renewable materials. Therefore, opting for suppliers who prioritize sustainable practices is crucial. This includes evaluating their production methods, energy consumption, and waste management strategies.
Ethical sourcing is paramount, as it not only aligns with global sustainability goals but also enhances brand reputation. Buyers should seek suppliers who adhere to ethical labor practices and have transparent supply chains. Certifications such as ISO 14001 (Environmental Management) and ISO 45001 (Occupational Health and Safety) can serve as indicators of a supplier’s commitment to sustainability and ethical practices.
Additionally, the use of “green” materials in CNC machine production is gaining traction. Materials that are recyclable or sourced from sustainable suppliers can significantly reduce the environmental footprint of manufacturing processes. B2B buyers should actively inquire about the certifications and sustainability initiatives of potential suppliers, ensuring that their sourcing decisions contribute positively to both their operational goals and broader environmental objectives.
Brief Evolution/History
The evolution of six-axis CNC machines can be traced back to the 1970s when CNC technology first emerged. Initially, these machines were limited to basic operations, but advancements in software and hardware have transformed them into highly sophisticated tools capable of complex tasks. The introduction of multi-axis machining allowed for increased precision and flexibility, making them indispensable in modern manufacturing.
In the early 2000s, the integration of computer-aided design (CAD) and computer-aided manufacturing (CAM) systems revolutionized the sector, enabling manufacturers to streamline processes and improve product quality. Today, six-axis CNC machines stand at the forefront of manufacturing innovation, combining speed, accuracy, and efficiency. This historical context is vital for B2B buyers as it underscores the technological advancements that can influence purchasing decisions and operational effectiveness in various industries.
Related Video: The Inside Story of the Ship That Broke Global Trade
Frequently Asked Questions (FAQs) for B2B Buyers of six axis cnc machine
-
What criteria should I use to vet suppliers of six axis CNC machines?
When vetting suppliers, consider their industry experience, customer reviews, and certifications. Look for suppliers with a proven track record in manufacturing six axis CNC machines and check their financial stability. Request references from previous clients, and assess their responsiveness and communication skills. Additionally, ensure they comply with international quality standards, such as ISO 9001, to mitigate risks associated with product quality and reliability. -
Can I customize a six axis CNC machine to meet specific needs?
Yes, many manufacturers offer customization options for six axis CNC machines. When discussing customization, clearly outline your operational requirements, such as specific materials, dimensions, and production volumes. Understand that custom features may affect pricing and lead times. It’s advisable to request a detailed proposal from the supplier that includes design specifications, cost implications, and timelines to ensure alignment with your business objectives. -
What are the typical minimum order quantities (MOQ) and lead times for six axis CNC machines?
MOQs can vary significantly depending on the supplier and the complexity of the machine. Generally, for specialized equipment like six axis CNC machines, MOQs can range from one unit to several units. Lead times typically span from 4 to 12 weeks, depending on customization and the supplier’s production capacity. Always confirm these details during initial discussions and factor them into your project timelines to avoid delays. -
What payment terms should I expect when purchasing a six axis CNC machine?
Payment terms can vary widely by supplier but generally include options such as upfront deposits (20-50%), followed by progress payments, and a final payment upon delivery. Some suppliers may offer financing options or letters of credit, especially for international transactions. Always negotiate terms that align with your cash flow and risk management strategies, and ensure that all agreements are documented clearly in the contract. -
How can I ensure the quality of the six axis CNC machine I am purchasing?
To ensure product quality, request detailed quality assurance documentation from the supplier, including inspection reports and certifications. If possible, arrange for a factory visit to observe the manufacturing process and quality control measures firsthand. Additionally, consider requesting a sample or a demonstration of the machine before finalizing the purchase to verify that it meets your specifications and performance expectations. -
What certifications should I look for in a six axis CNC machine?
Key certifications to look for include ISO 9001 for quality management systems, CE marking for compliance with European safety standards, and specific industry certifications like UL for electrical safety. These certifications indicate that the supplier adheres to recognized quality and safety standards, which is crucial for minimizing operational risks and ensuring compliance with regulatory requirements in your region. -
What logistics considerations should I keep in mind when importing a six axis CNC machine?
Logistics can be complex when importing machinery. Factors to consider include shipping methods (air vs. sea), customs duties, insurance, and delivery timelines. Collaborate with a logistics partner familiar with international trade regulations and customs procedures in your country. Additionally, ensure that the supplier provides necessary shipping documentation and compliance with local import regulations to avoid costly delays.
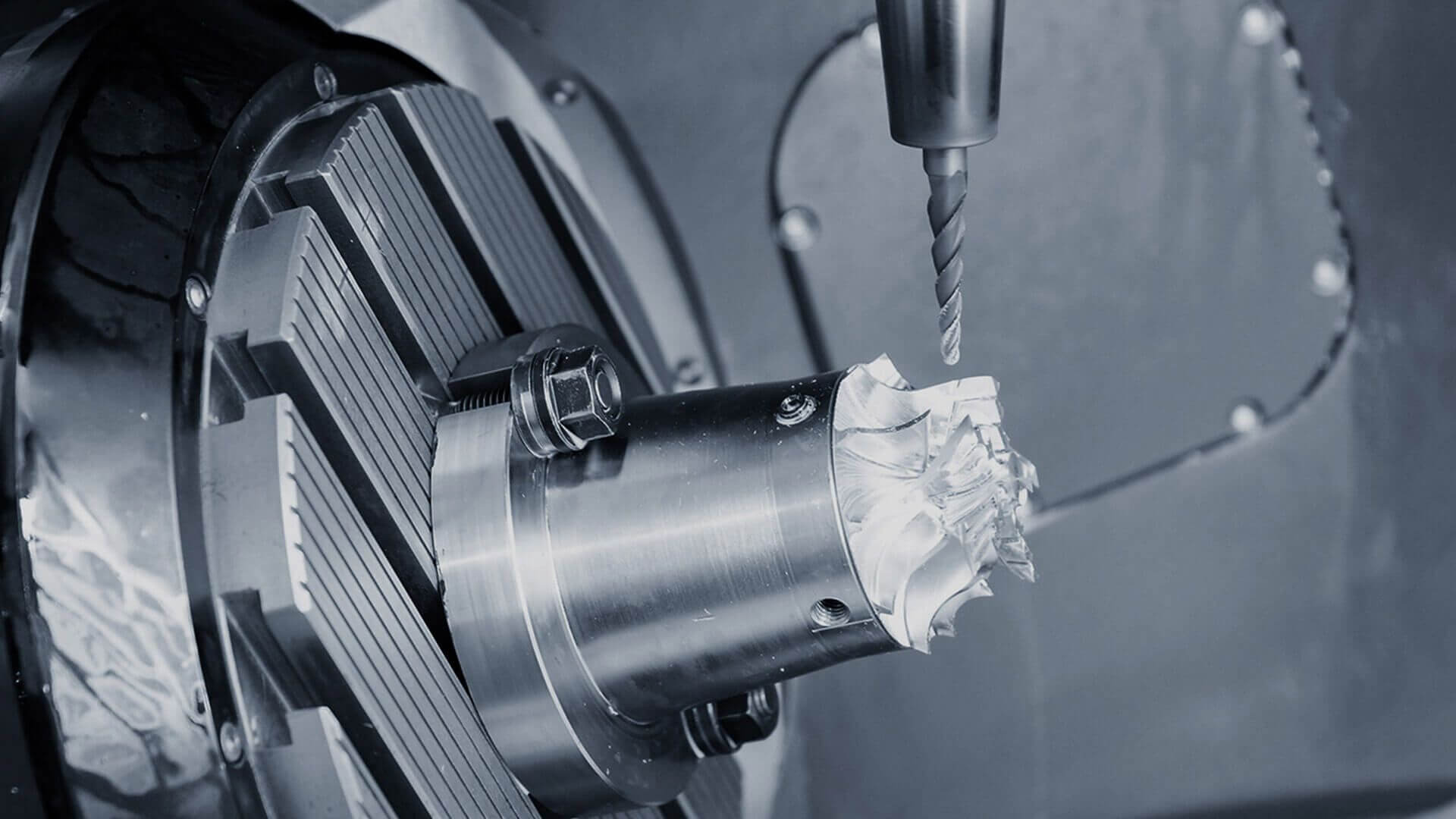
Illustrative Image (Source: Google Search)
- How should I handle disputes with suppliers of six axis CNC machines?
To manage disputes effectively, establish clear communication channels and document all agreements in the contract, including dispute resolution mechanisms. If issues arise, attempt to resolve them amicably through direct negotiation. If that fails, consider mediation or arbitration as outlined in your contract. It’s beneficial to consult with a legal expert familiar with international trade laws to understand your rights and obligations in the event of a dispute.
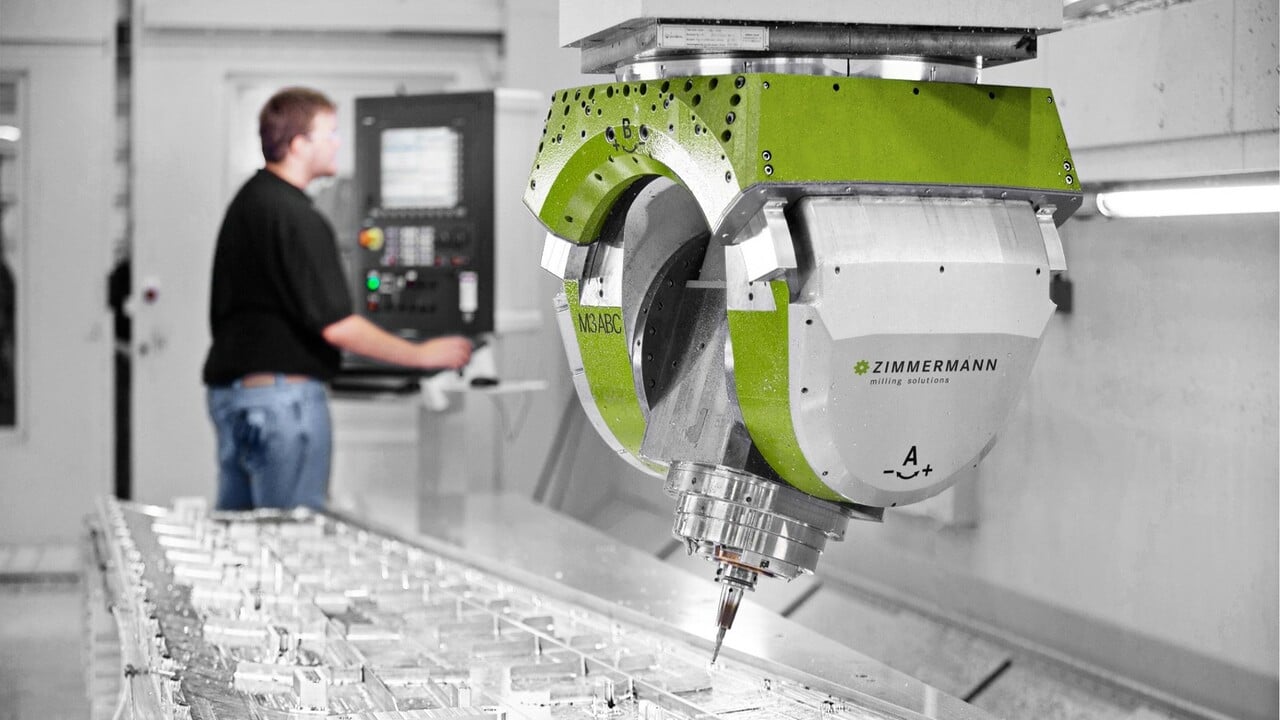
Illustrative Image (Source: Google Search)
Important Disclaimer & Terms of Use
⚠️ Important Disclaimer
The information provided in this guide, including content regarding manufacturers, technical specifications, and market analysis, is for informational and educational purposes only. It does not constitute professional procurement advice, financial advice, or legal advice.
While we have made every effort to ensure the accuracy and timeliness of the information, we are not responsible for any errors, omissions, or outdated information. Market conditions, company details, and technical standards are subject to change.
B2B buyers must conduct their own independent and thorough due diligence before making any purchasing decisions. This includes contacting suppliers directly, verifying certifications, requesting samples, and seeking professional consultation. The risk of relying on any information in this guide is borne solely by the reader.
Strategic Sourcing Conclusion and Outlook for six axis cnc machine
In conclusion, the strategic sourcing of six-axis CNC machines presents significant opportunities for international B2B buyers, particularly in regions such as Africa, South America, the Middle East, and Europe. By focusing on quality, supplier reliability, and local market conditions, buyers can ensure they select the right partners to enhance their operational capabilities. Key takeaways include the importance of conducting thorough supplier assessments, understanding the specific needs of your manufacturing processes, and leveraging technology for better supply chain management.
Value of Strategic Sourcing:
– Cost Efficiency: Effective sourcing strategies can lead to reduced operational costs.
– Quality Assurance: Partnering with reputable manufacturers ensures high-quality outputs.
– Innovation Access: Collaborating with advanced suppliers can lead to innovative solutions tailored to your business needs.
As the global manufacturing landscape continues to evolve, it is essential for B2B buyers to stay informed about emerging trends and technologies in CNC machining. The future holds vast potential for growth and efficiency, particularly for businesses willing to adapt and invest in the right machinery. Engage with suppliers who understand your market and can provide tailored solutions. Take proactive steps today to secure a competitive advantage for tomorrow.